Unreinforced Amorphous PEI for Medical Devices & Pharmaceutical Applications
SABIC’s new Ultem HU resins help manufacturers choose alternatives to ethylene oxide sterilization.
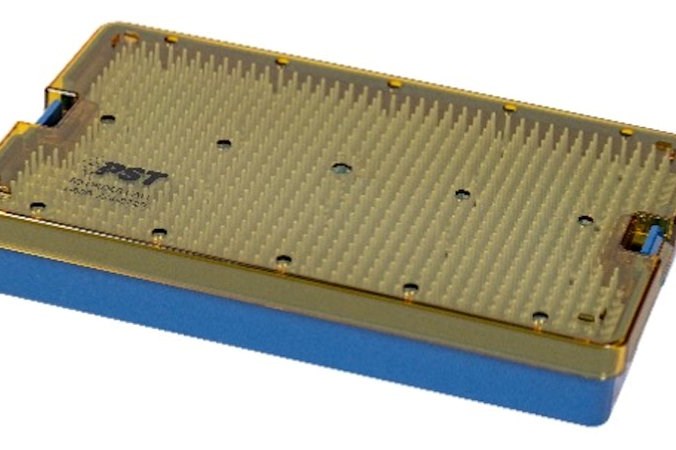
A new family of biocompatible (ISO 10993 or USP Class VI , unreinforced amorphous PEI (polyetherimide) resins from SABIC can help manufacturers of medical devices and pharmaceutical applications choose alternatives to ethylene oxide (EtO) sterilization. This in anticipation of a new ruling by the U.S. Environmental Protection Agency (EPA) that may reduce EtO emissions from commercial sterilization facilities, which has increased demand for materials compatible with other sterilization methods.
Ultem HU resins are stable across many popular sterilization processes including, vaporized hydrogen peroxide (VHP) gas plasma, steam autoclave, gamma radiation, electron beam, X-ray and ultraviolet-C. Moreover, they have been shown to retain their high strength, dimensional stability and attractive aesthetics such as color retention, under exposure to repeated sterilization cycles. This can help reduce breakage and discoloration, thereby potentially extending the useful life of applications made with these materials. According to the U.S. Food and Drug Administration (FDA), approximately 50% of sterile medical devices are treated with EtO, totaling about 20 billion devices each year. EPA’s proposed rule would reduce EtO emissions by an estimated 80 percent.
Related Content
-
Medical Molder, Moldmaker Embraces Continuous Improvement
True to the adjective in its name, Dynamic Group has been characterized by constant change, activity and progress over its nearly five decades as a medical molder and moldmaker.
-
First Water Bottles With Ultrathin Glass Coating
Long used for sensitive juices and carbonated soft drinks, KHS Freshsafe PET Plasmax vapor-deposited glass coating is now providing freshness and flavor protection for PET mineral water bottles.
-
PHA Compound Molded into “World’s First” Biodegradable Bottle Closures
Beyond Plastic and partners have created a certified biodegradable PHA compound that can be injection molded into 38-mm closures in a sub 6-second cycle from a multicavity hot runner tool.