‘Ultrafast’ Machine for Large PET Bottles
Sidel’s new EvoBLOW XL stretch blow molder makes up to 10 L PET bottles at up to 18,000 bph.
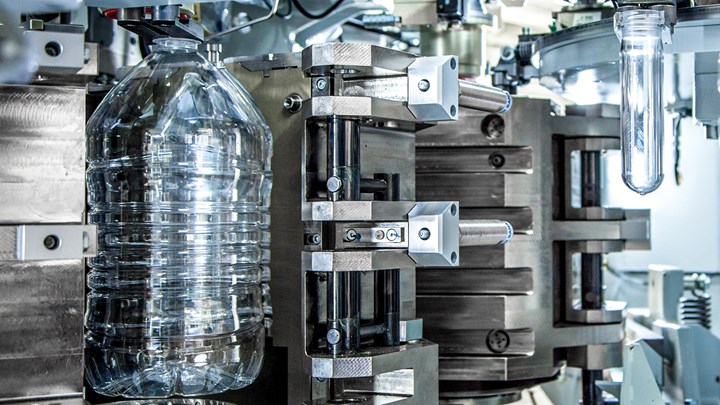
Sidel’s EvoBLOW XL features an embedded mold-handling tool, mobile mold storage unit and “proven” 98% OEE. Photo Credit: Sidel
The EvoBLOW range of rotary reheat stretch blow machines from Sidel formerly was sized for PET bottles up to 3.5 L size. Sidel’s EvoBLOW XL machine extends that range up to 10 L. Described as “ultrafast,” this new model produces up to 18,000 bph with a “proven” 98% Overal Equipment Effectiveness (OEE).
The XL machine has 75% of parts in common with the rest of the EvoBLOW range. It has an ergonomic, embedded mold-handling tool that’s said to simplify position of heavy molds and ensure safety. The mobile mold storage unit provides fast and safe access to molds close to the machine. Newly designed blowing circuits and valves help reduce energy consumption. The XL model can integrate with other Sidel solutions such as its latest ultrafast changeover system, Bottle Switch. It also can connect with Sidel’s Evo-ON cloud software for predictive maintenance and monitoring of energy consumption and productivity performance.
The XL machine can handle up to 100% rPET. It has flexible oven configurations and a wide choice of bottleneck dimensions. It can function as a stand-alone or integrated combi solution for filling and capping. Work is underway to extend the XL technology to hot-fill products.
Related Content
-
How to Extrusion Blow Mold PHA/PLA Blends
You need to pay attention to the inherent characteristics of biopolymers PHA/PLA materials when setting process parameters to realize better and more consistent outcomes.
-
Foam-Core Multilayer Blow Molding: How It’s Done
Learn here how to take advantage of new lightweighting and recycle utilization opportunities in consumer packaging, thanks to a collaboration of leaders in microcellular foaming and multilayer head design.
-
Get Color Changes Right In Extrusion Blow Molding
Follow these best practices to minimize loss of time, material and labor during color changes in molding containers from bottles to jerrycans. The authors explore what this means for each step of the process, from raw-material infeed to handling and reprocessing tails and trim.