Slimmer All-Electric Press Debuts
NPE2024: A slimmed-down version of Engel’s all-electric, e-mac injection molding machine is among eight displays, which also include LSR micromolding, quick mold changes and a cube mold.
A thinner version of Engel’s all-electric, e-mac injection molding machine is debuting at NPE2024, providing molders with width reduction of up to 16%. At the show, an e-mac 1565/310 is molding a bottle tray from a single-cavity mold supplied by Haidlmair. Engel says despite the thinner profile, the slim e-mac offers the same mold space as standard versions and the ability to accommodate large molds like the bottle tray. Equipped with a recycling package consisting of a highly abrasion- and corrosion-resistant screw as well as a melt filter, the e-mac will mold the trays at the show from regrind.
A hybrid Engel e-speed 610/90 designed for high-speed packaging applications is running a 4+4 family stack mold producing tamper-evident food containers and lids. Applying in-mold labeling (IML) and two significantly different part sizes, the machine’s hybrid design enables high injection pressures and speeds with very short injection strokes.
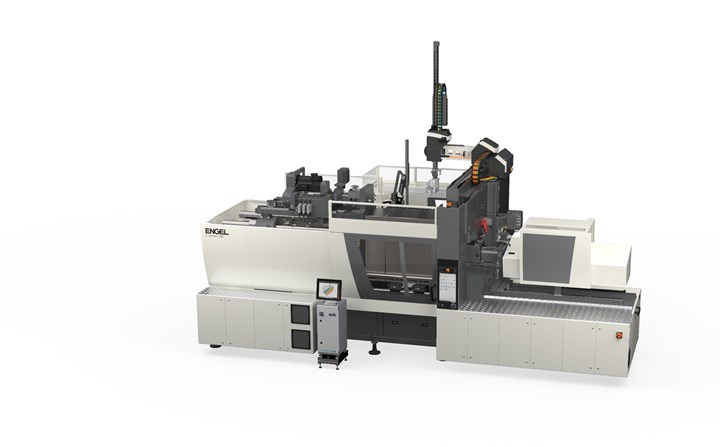
At NPE2024 the new e-mac 1565/310 will mold a bottle tray from regrind using a Haidlmair mold.
Source: Engel
Nexteco, which was acquired by Top Grade Molds in 2018, creates what it calls stack mold harmonic arm-centering devices. Mold or machine mounted, the synchronized centering device can be optimized for family molds with asymmetrical opening, minimizing machine clamp stroke and cycle time. At the Engel booth, a Nexteco asynchronous mold-carrier system, complemented by an integrated water manifold, enables simultaneous molding of both containers and lids. In addition to the tool, Top Grade Molds also supplied its Modular Mold Change system for swift product changeovers. Automation is provided by Campetella, with vision inspection by Mevisco, labels by MCC Verstraete, Frigel process cooling and resin from Washington Penn.
In a , an 80-ton tiebarless hydraulic victory 330/85 is applying a Stäubli QMC quick-clamping system. The two molds to be swapped in and out are from Roembke Mfg. & Design and will mold salad tongs and a fruit bowl, respectively, from Shell HDPE. Using RFID for mold identification, the machine automatically adopts the correct process parameters for the new mold upon switching without operator intervention. The iQ weight control automatically adjusts the process parameters to account for material property fluctuations and changes in ambient conditions, shot by shot. An Engel viper 12-linear robot removes the parts with end-of-arm tooling which is also identified using RFID and exchanged via quick coupling.
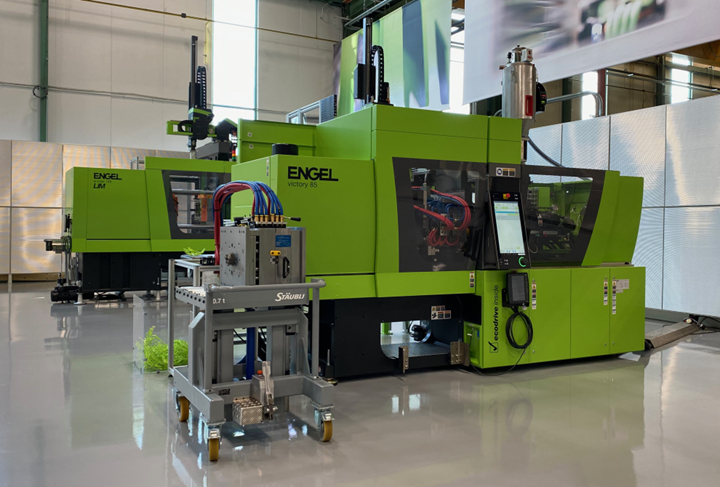
Engel and Staubli will demonstrate quick mold changes using a Roembke tool on a Engel victory 330/85. Source: Engel
Two-component diagnostics cartridges are being molded in cleanroom conditions on an all-electric e-motion 440H/160TWP combi M running a cube mold on a horizontal rotary table.
Engel says this fully integrated production cell showcases the potential for maximum production from minimal space, thanks in part to the dual-face mold, with 32 cavities each, from Hack Formenbau. The indexing table in the combi M design divides the machine’s mold-closing area in the center to enable production from both tool faces in parallel. In this setup, the secondary injection unit is situated on the moving platen.
Two robots also work in parallel to remove and pack the cartridges. An Engel viper 20-linear robot takes the two-component parts from the machine and deposits them in trays, while an Engel e-pic pick-and-place robot stacks the fully populated trays with an intermediate layer into boxes and then discharges them via an integrated tray server.
In LSR, Engel is showcasing micromolding of valves weighing just 0.001 g. Partnering with ACH Solution, a tiebarless all-electric Engel e-motion 50/30 TL with a microinjection unit molds the LSR valves from a 32-cavity tool. A viper 12-linear robot working with an optical testing unit by ACH Solution, ensures precise handling and inspection of the microcomponents. The iQ weight control validates consistent shot weights despite any viscosity differences in the two-component LSR material from Wacker.
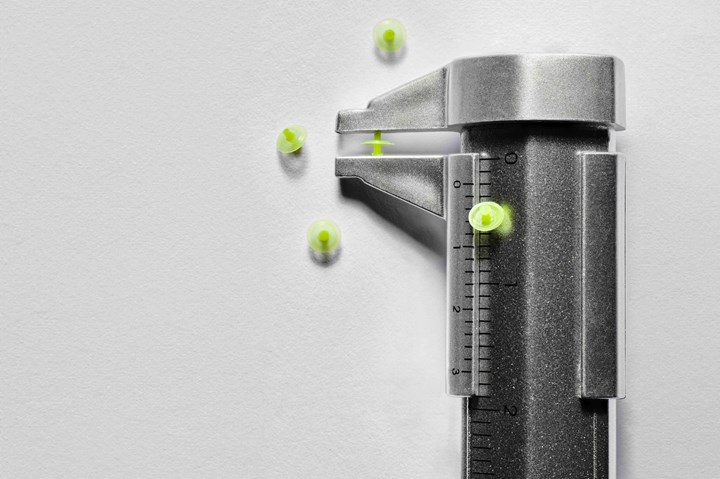
Engel will partner with ACH Solution to mold 0.001g microvalves from LSR on a 32-cavity tool.
Source: Engel
A servo-hydraulic, two-platen duo 770 WP tech U.S. machine is showcasing the production and decoration of automotive components. The large-area sliding table mold from Schöfer will mold a front panel in a single cycle using Engel foilmelt and clearmelt technologies. Translucent polypropylene from SABIC is joined with polyurethane (PUR) from Ruehl for cost and weight savings, by applying a Kurz inmold decoration (IMD) film. PUR dosing equipment comes from Italy’s Cannon. The process combines decoration and scratch-resistant surface creation through IMD and PUR coating, resulting in a part with electromagnetic transparency. The fully integrated production cell utilizes easix automation.
Six years since its NPE2018 debut, the Wintec line is being presented via an 830-ton t-win 750/7800. The machine is molding garage floor tiles from 100% recycled ocean waste, using an integrated Engel viper 40-linear robot for part removal. Here again, the iQ weight control simplifies the use of recycled materials. Wintec customer CH3 Solutions supplies the mold for this cell, with raw material from Chilean firm Atando Cabos, which takes on ocean waste by recycling discarded fishing ropes in Patagonia. ExxonMobil supplies material and additives for enhanced processing.
In addition to Engel’s booth, the company has machines running at partner exhibits as well. At the Canadian Association of Moldmakers (CAMM), an e-motion 44/180 WP is molding flip-top closures from a Cap-Thin Molds tool. LSR supplier Wacker is featuring a flexseal 300 with rotofeeder molding a lemon press from silicone. Ilsemann Automation is molding a petri dish on an e-motion 2440/420 T – US, and Vasantha Tool Crafts PVT Ltd. is using an e-mac 50/90 US to mold 1-mL syringe.
Related Content
In-Mold Labeling Applied to Medical
In collaboration with multiple partners, Arburg will showcase IML for centrifuge tubes at Fakuma 2023, eliminating printing or other downstream steps.
Read MoreKurz Opens New Plant in Vietnam
The maker of decorative thin films invested 37 million euros in the new 60,000-m2 plant in Quy Nh啤n, which joins regional production facilities in China and Malaysia.
Read MoreCompletely Connected Molding
NPE2024: Medical, inmold labeling, core-back molding and Industry 4.0 technologies on display at Shibaura’s booth.
Read MoreBreaking News From NPE2024
Here is a firsthand report of news in injection molding, extrusion, blow molding and recycling not previously covered.
Read MoreRead Next
People 4.0 – How to Get Buy-In from Your Staff for Industry 4.0 Systems
Implementing a production monitoring system as the foundation of a ‘smart factory’ is about integrating people with new technology as much as it is about integrating machines and computers. Here are tips from a company that has gone through the process.
Read MoreFor PLASTICS' CEO Seaholm, NPE to Shine Light on Sustainability Successes
With advocacy, communication and sustainability as three main pillars, Seaholm leads a trade association to NPE that ‘is more active today than we have ever been.’
Read MoreLead the Conversation, Change the Conversation
Coverage of single-use plastics can be both misleading and demoralizing. Here are 10 tips for changing the perception of the plastics industry at your company and in your community.
Read More