Redesigned Rotary Level Indicator
Red enclosure now rotates once installed to help ensure conduit entries are always pointed toward the ground, mitigating the risk of moisture damaging internal components.
BinMaster has redesigned its BMRX-100 rotary level indicator, which is an electromechanical device used in solids and powders to prevent material bin overfills, dry runs, or to shut off a process.
In the new iteration, BinMaster has designed the new red enclosure to rotate once installed. This feature helps ensure conduit entries are always pointed toward the ground, mitigating the risk of moisture damaging internal components. The “conduits down” feature makes proper installation simple and leads to a long service life. Another new rotary feature incorporates a wire guide that ensures wires don’t get stuck as you push them through conduit entries.
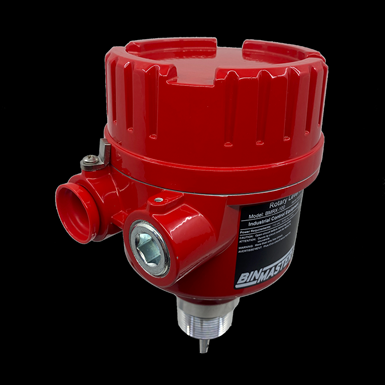
Photo: BinMaster
The BMRX-100 can be used for process control by wiring it to a light or horn to alert status has changed from uncovered to covered or vice versa. This bin indicator can alert to high levels to prevent spills. Or it can be mounted low in the bin to know when it’s almost empty to prevent batching errors and dry runs. It also can be deployed o detect overloaded or empty conveyors, or let you know when a chute gets clogged with material.
The BMRX-100 power pac sells for under $300 and is available on the BinMaster website or from a local distributor. It can also be ordered with optional process connections if the level sensor is used in corrosive or caustic material. It can be specified with a choice of 19 steel and plastic paddles suitable for light to heavy materials. Popular collapsible paddles simplify installation since no bin entry is required. It can also be used as a top-mounted level detector when custom-ordered with galvanized or stainless-steel extensions.
Related Content
-
Service Enables One-Day Auxiliary Commissioning
One-day, on-site equipment setup and training assistance program for all types of Conair auxiliaries.
-
How to Effectively Reduce Costs with Smart Auxiliaries Technology
As drying, blending and conveying technologies grow more sophisticated, they offer processors great opportunities to reduce cost through better energy efficiency, smaller equipment footprints, reduced scrap and quicker changeovers. Increased throughput and better utilization of primary processing equipment and manpower are the results.
-
Technology Aims to Smarten Up Resin Conveying
At NPE2024, Novatec moves to rewrite the rules for material conveying with patent-pending smart-pump technology.