Modular Feeding System
Gearing units on both feeders to be easily and quickly changed and removed and replaced in just a few steps.
At Fakuma 2021 Friedrichshafen, Germany, in Brabender Technologie will introduce two modular feeders: the twin-screw DDSR20 2.0 (photo) and the single-screw DSR28 2.0.
The modular design allows the gearing units on both feeders to be easily and quickly changed and removed and replaced in just a few steps, enabling users to switch between large and small models or from single to twin-screw versions. The screw hopper is located at the front edge of the scale and the screw trough can now easily be removed from the front of the feeder. The company says this has greatly enhanced the feeder accessibility, and end users benefit from the ease and speed of cleaning components that come into ingredient contact.
In the new designs, seal replacement is also reportedly much easier and faster thanks to the trough, which can be removed from the front of the feeder: a new seal can be inserted within five minutes, with special versions for ATEX, food and pharma, depending on requirements. The newly installed seal-change indicator can indicate the need to change seals at an early stage, thus preventing gear and motor damage. In addition, all Generation 2.0 units feature dust-tight vertical outlets made of food-grade, transparent PETG. This hard plastic is characterized by its high transparency and shatterproof construction enabling the operator to perform visual checks inside the screw tube.
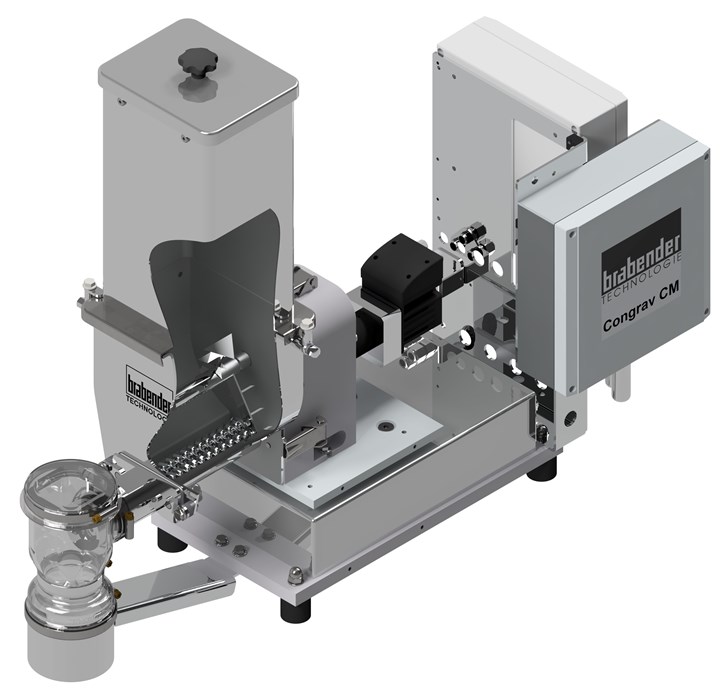
All Generation 2.0 units are also available with a servo motor on all models. This servo motor has the added benefit that when compared to normal frequency-controlled motors, they have a much wider speed range and have full power available even at low rpm. The need to change screws and screw tubes can now be eliminated reducing downtime, Brabender says. At lower speeds, servo motors can start close to full torque and even in high torque conditions they continue to have excellent speed control.
Related Content
-
Smart Works Cells at the Heart of Wittmann’s Exhibit
NPE2024: Under the theme of “It's All Wittmann,” the supplier of injection molding machines, automation and auxiliary equipment is hoping to show NPE attendees what comes with true connectivity.
-
Service Enables One-Day Auxiliary Commissioning
One-day, on-site equipment setup and training assistance program for all types of Conair auxiliaries.
-
LSR Molding Dosing System Designed for Precision, Efficiency and Compliance
The system offers a variety of features to successfully produce high-quality silicone parts with the most economic use of material, space, working time and energy.