Miniature Melt Pressure Sensor Takes Measurements Directly in the Nozzle
Kistler says the ultra-compact Type 4004A piezoresistive pressure and temperature sensor can be applied in hot runners and 3D printing applications.
Kistler has introduced the new Type 4004A piezoresistive melt pressure sensor, featuring a front diameter of 3 mm, which allows it to operate directly in injection nozzles and small extruders. In these spaces, it can measure both pressure and temperature in direct contact with the plastic melt, with potential applications in hot runner systems and additive manufacturing.
With an operating and measurement range of up to 350°C, the 4004A melt pressure sensor can be used directly in the hot runner to deliver precise measurements of pressure and temperature in injection nozzles and extruders.
For the two different processes, the 4004A features two separately calibrated pressure ranges, going up to 2500 bar (36,000 psi) for hot runners and up to 1000 bar (14,500 psi) for additive manufacturing. Changes in the pressure signal could detect debris in small nozzles, wear in the nozzle or melt backflow.
Access to key parameters comes via TEDS (Transducer Electronic Data Sheet), and since the sensor’s diaphragm is made of hardened steel with an IP65 degree of protection, the 4004A can be used for applications involving fiber-reinforced plastics. It can also be operated in medical and food packaging sectors since no oil or mercury are used to transmit the signals.
The temperature-compensated pressure signal can be accessed via the analog output or the sensor's RS232 interface. This allows it to connect to Kistler’s ComoNeo process monitoring system.
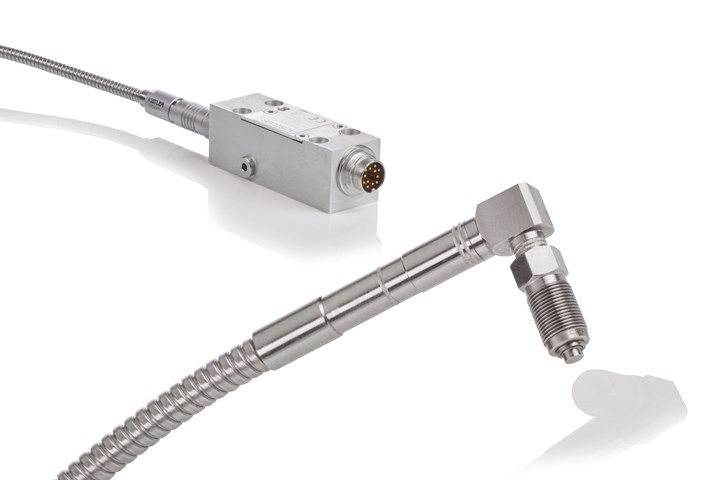
The new 4004A miniature melt pressure sensor from Kistler allows for measuring pressure and temperature directly in the hot runner at temperatures up to 350°C.
Photo Credit: Kistler
Related Content
-
Additive Fusion Technology Optimizes Composite Structures for Demanding Applications
9T Labs continues to enhance the efficiency of its technology, which produces composite parts with intentionally oriented fibers.
-
NPE 2024: Additive Manufacturing Assisting, Advancing Plastics Processing
Exhibitors and presenters at the plastics show emphasized 3D printing as a complement and aid to more traditional production processes.
-
How 3D Printing Supports Toolmaking Workforce at This Multiscale Molder
At more than a century old, General Pattern has seen multiple evolutions in its 大象传媒 — the latest of which is the embrace of additive manufacturing technologies for mold tooling and beyond.