Large Electric Shuttle for Coextrusion with PCR
At K 2022, Plastiblow showed the new all-electric PB50ES-1000 Coex3 machine making three-layer, 20 L jerrycans with PCR in the center layer.
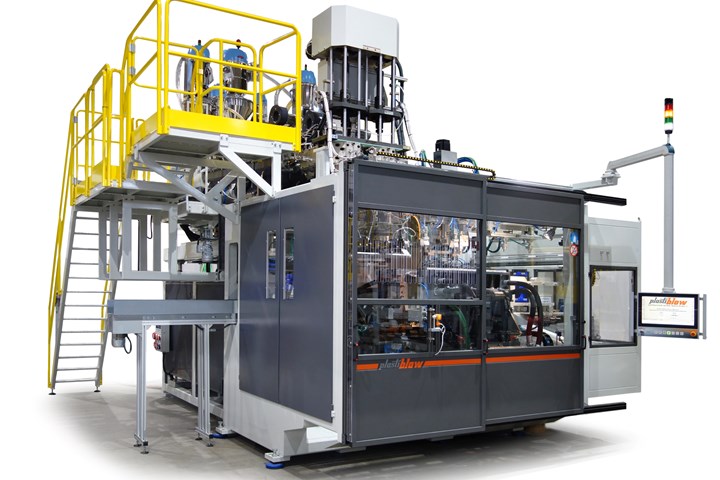
Brand-new PB50ES-1000 Coex3 all-electric shuttle from Plastiblow for three-layer coextrusion with PCR. (Photo: Plastiblow)
At the recent K 2022 show in Düsseldorf, of Italy (represented here by Globeius) introduced what it calls the “all-new” model PB50ES-1000 Coex machine for three-layer coextrusion blow molding with post-consumer recycle (PCR). The all-electric, continuous-extrusion shuttle has a 50-metric-ton (55 U.S. ton) clamp and 1000-mm stroke (a model with 1300-mm stroke is also offered). The largest size of the company’s all-electric shuttles, it comes with “Industry 4.0 ready” controls that allow for remote monitoring and diagnosis.
At the show, the machine made stackable 20-liter HDPE jerrycans in two cavities with three layers, the center layer of PCR. The single-sided machine has a maximum output over 240 jerrycans/hr, which can be doubled in a model with two heads and two stations. The machine on display had three horizontal extruders, one of 100-mm diam. for the center PCR layer and two of 80-mm for the inner and outer layers. The dual three-layer coex head had a 200-mm die and 400-mm center distance with dynamic PWDS ring device for parison thickness control and radial optimization. The two-cavity mold had a movable bottom section, driven by electric servomotors.
Related Content
-
PolyJohn Turns to Blow Molding, Doubles Its Productivity
Leading maker of portable sanitation products knew thermoforming, sheet extrusion, rotomolding and injection molding. Then it found the missing link to higher productivity and new markets: blow molding.
-
Processing Megatrends Drive New Product Developments at NPE2024
It’s all about sustainability and the circular economy, and it will be on display in Orlando across all the major processes. But there will be plenty to see in automation, AI and machine learning as well.
-
Blow Molder with a Mission: CKS Packaging Shares Gains Of Its Phenomenal Growth
From three machines in 1986 to 27 plants nationwide today, this family-owned processor has prospered through unwavering customer service, committed employees and dedicated service to its community.