Injection-Blow Tooling System Reduces Labor, Improves Quality
Liberty IBM System is said to overcome long-standing limitations of injection-blow tooling.
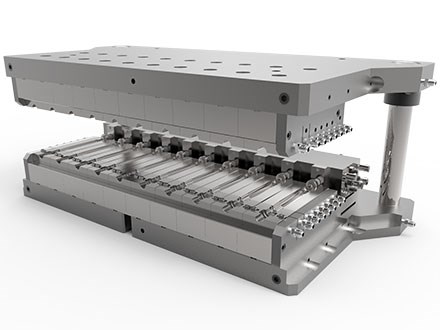
The Liberty IBM System achieves thermal isolation between the neck insert and the shoulder of the bottle. (Photo: R&D/Leverage)
For more than 40 years, R&D/Leverage has developed tooling solutions for injection molding and stretch-blow molding. When the firm began building tooling for the injection-blow molding (IBM), it found an opportunity to make improvements to the traditional design of injection blow tools. The company set out to identify and resolve problems related to traditional injection blow tooling.
The result is the Liberty IBM System, announced last year. It uses patented technology to overcome the challenges of conventional IBM tooling. R&D/Leverage filed its 15th IBM-related patent this year, as its solutions keep evolving to make better injection-blow tooling.
“The reason we became so interested in improving the IBM tooling is that when we got into that 大象传媒 we recognized there were many problems inherent in the traditional design that were not conducive to cost-effective manufacturing and productivity that today’s injection-blow molders need to be competitive in their markets. Because of these design problems in IBM, especially for startup of a run, it was very labor intensive,” says Jeff Chen, Director of Research & Simulation at R&D/Leverage.
Some of the problems inherent in a conventional IBM tool that the Liberty IBM System solves are said to include the following:
It eliminates thermal-expansion related problems like bowing of the die-set.
It enables process technicians to do “cold starts” without having to torch the nozzles.
It minimizes thermal-expansion-induced wear at the nozzle tip and gate area, which also eliminates frequent replacement of the nozzle.
It eliminates the need to engage and disengage the manifold from the injection cavity for startup and shutdown.
It enables easier achievement of a high degree of manifold balance.
It minimizes temperature bleed-over between neck insert and cavity.
It offers a solution to the galling and wear of traditional bottom-mold retract components by utilizing a new retract system.
It minimizes parting-line mismatch.
A major improvement of the Liberty IBM System is said to be its ability to achieve thermal isolation between the neck insert and the shoulder of the bottle. Unlike traditional IBM tools that use key stock and all-thread to locate and clamp the mold inserts onto the die set, the Liberty IBM System uses dowels to locate the mold inserts. This allows gaps to be designed between the mold inserts, which negate the effects of accumulated horizontal thermal expansion across the injection mold inserts.
The Liberty Sytem also incorporates a new, patent-pending Self-Alignment System that is said to ensure optimal cavity alignment in the parison and blow stations. These new technologies reportedly allow fast and trouble-free startups, improved bottle quality, and reduced tool wear. The new system can be designed to change out damaged cavities without removing the tool from the machine.
R&D/Leverage currently has 16 Liberty IBM Systems running in the field with up to 38 cavities. “The higher cavitation tools will have the highest return for our customers, based on ease of start-up and tool maintenance,” says Bruce Wardlow, dir. of product development.
Another benefit of the Liberty IBM System is that it helps bridge the skills gap. “By making the tool more predictable, a process technician with less experience can run the system,” says Wardlow.
Related Content
First Water Bottles With Ultrathin Glass Coating
Long used for sensitive juices and carbonated soft drinks, KHS Freshsafe PET Plasmax vapor-deposited glass coating is now providing freshness and flavor protection for PET mineral water bottles.
Read MoreThe Recycling Collaboration That Is Making Circular Film a Reality
Nova Chemicals and Novolex are commissioning a large mechanical recycling facility for film to film.
Read MoreFoam-Core Multilayer Blow Molding: How It’s Done
Learn here how to take advantage of new lightweighting and recycle utilization opportunities in consumer packaging, thanks to a collaboration of leaders in microcellular foaming and multilayer head design.
Read MoreGet Color Changes Right In Extrusion Blow Molding
Follow these best practices to minimize loss of time, material and labor during color changes in molding containers from bottles to jerrycans. The authors explore what this means for each step of the process, from raw-material infeed to handling and reprocessing tails and trim.
Read MoreRead Next
See Recyclers Close the Loop on Trade Show Production Scrap at NPE2024
A collaboration between show organizer PLASTICS, recycler CPR and size reduction experts WEIMA and Conair recovered and recycled all production scrap at NPE2024.
Read MoreLead the Conversation, Change the Conversation
Coverage of single-use plastics can be both misleading and demoralizing. Here are 10 tips for changing the perception of the plastics industry at your company and in your community.
Read More