Conveyors Feature New Line of Controllers
Sensor-based design monitors material levels in the feed hopper, vacuum conveyor, and/or receiving vessel via a choice of three operating modes, automatically controlling material transfer at every step.
Bristol, Pennsylvania, has unveiled a line of advanced controllers that automatically manages operation of the company's pneumatic vacuum conveying systems. Applying proprietary technology, the ET line of conveyor controllers features a sensor-based design that monitors material levels in the feed hopper, vacuum conveyor, and/or receiving vessel via a choice of three operating modes, automatically controlling material transfer at every step. The potential for human error is eliminated and peak conveying efficiency assured.
Suitable for managing the transfer of powders, pellets, granules, and other bulk materials, the ET line of electronic controllers comprises the ET-Advance for monitoring up to four level sensors at the same time, and the ET3 and ET4 for monitoring a choice of individual sensor locations. The intelligent controllers may be adjusted to change the vacuum pump suction time, material discharge time, line clearing time, and other parameters to quickly accommodate different materials and recipes.
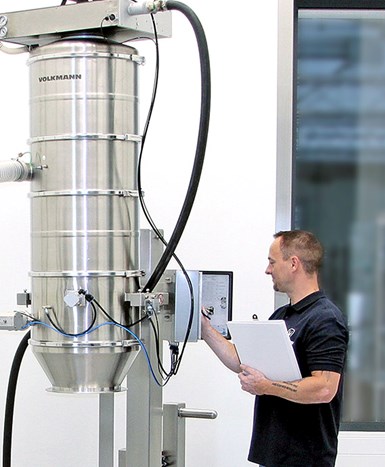
The ET controllers may be integrated into existing PLC environments or operated as standalone units. Testing is offered on a fully operating conveying system in the company's facility.
Related Content
-
PTXPO Recap: Smarter Resin Drying & Conveying Automation
Check out what you missed on the PTXPO show floor. In this video, Editorial Director Jim Callari breaks down how AI is changing the game in plastics manufacturing.
-
Service Enables One-Day Auxiliary Commissioning
One-day, on-site equipment setup and training assistance program for all types of Conair auxiliaries.
-
Cut Loading Time Through Direct Charge Blending
Direct charge blender loading, a vacuum-powered automation process, can dramatically improve loading time and reduce material costs. In this article, we address ten common questions to help you determine if the systems are right for your facility.