Clean-Room Ready Molding Machine
Boy says all the functions required for automated cleanroom production—including laminar air flow and part packaging—can be placed within the machine’s footprint.
German injection molding machine manufacturer Dr. Boy GmbH & Co. KG (U.S. offices in Exton, Penn.) will introduce the clean-room ready injection molding machine at the taking place April 20-22 and organized from Nuremberg, Germany.
The machine’s cantilevered two-platen clamping unit reportedly provides a number of space-saving design advantages, especially for medical technology. Featuring a compact footprint to help medical molders maximize clean room space, the machine can fit all of the functions required for automated cleanroom production within its frame. Examples of this include the laminar flow box, which is positioned above the clamping unit, while beneath the cantilevered clamping unit, there is space for packaging equipment allowing the direct bagging of molded parts as they’re produced
The machine control has an integrated start-up circuit to separate out a run’s first parts for inspection. At the machine’s base, molders can choose greater ground clearance as an option to ease cleaning. The machine also features an anti-static coating to eliminate particulate attraction.
A Boy spokesperson told Plastics Technology that any tonnage of the company’s machines can equipped with the clean room design, from 10 to 127 tons. Shot sizes range from 15.3 to 339.8 cm3. In terms of footprint, the range is from 0.78 to 5.22 m2.
The MedtecLIVE online-Portal features chat functions to allow visitors to converse directly with Boy representatives.
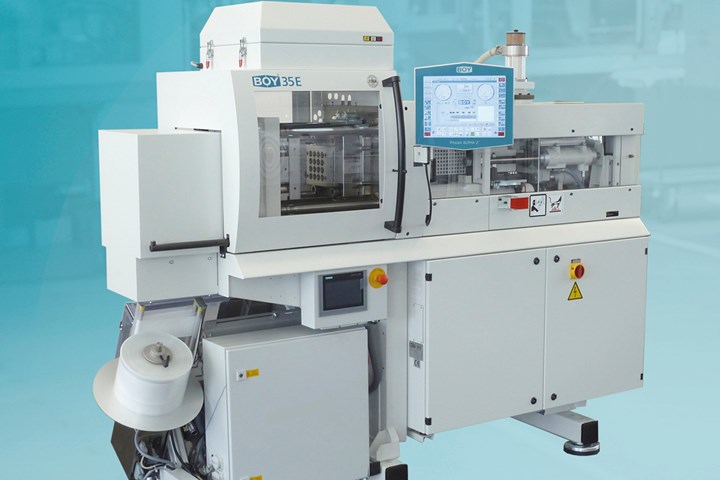
Boy Machines’ clean room ready injection molding machine features a laminar air flow unit above the clamp and automated bagging system below.
Related Content
-
PHA Compound Molded into “World’s First” Biodegradable Bottle Closures
Beyond Plastic and partners have created a certified biodegradable PHA compound that can be injection molded into 38-mm closures in a sub 6-second cycle from a multicavity hot runner tool.
-
Impacts of Auto’s Switch to Sustainability
Of all the trends you can see at NPE2024, this one is BIG. Not only is the auto industry transitioning to electrification but there are concerted efforts to modify the materials used, especially polymers, for interior applications.
-
First Water Bottles With Ultrathin Glass Coating
Long used for sensitive juices and carbonated soft drinks, KHS Freshsafe PET Plasmax vapor-deposited glass coating is now providing freshness and flavor protection for PET mineral water bottles.