Spectrum Plastics Expands Cleanroom, Boosts Production Capacity
The company completed a major renovation of its Minneapolis facility, including additional injection molding and cleanroom capacity.
Spectrum Plastics Group (Alpharetta, Ga.) has just completed a major renovation and cleanroom expansion at its Minneapolis facility. The company stated in a press release that continued growth in implantable and medical components required an investment in additional cleanroom capabilities.
Improvements to the 105,000-ft2 facility include additional molding machine capacity, renovation of office and employee amenity space, and what the company described as “additional updates that reflect the modern state-of-the-art and highly technical molding services we provide our customers.”
The new, unspecified number of injection molding machines are electric, and mostly offer 110 tons or less of clamping force. The Class 8 cleanroom manufacturing space was expanded to a total of 10,000-ft2. Resin drying occurs outside the cleanroom and high-purity nitrogen and oil-free compressed air are used to reduce risk of contamination. Real-time data capture, process quality monitoring, and in-cavity pressure monitoring are all utilized in the molding operations.
Spectrum Plastics Group has 20 locations and more than 1 million square feet of manufacturing space across six countries, with capabilities in extrusion; injection molding; blown film extrusion and conversion; medical balloon fabrication; laser processing; additive manufacturing; and assembly.
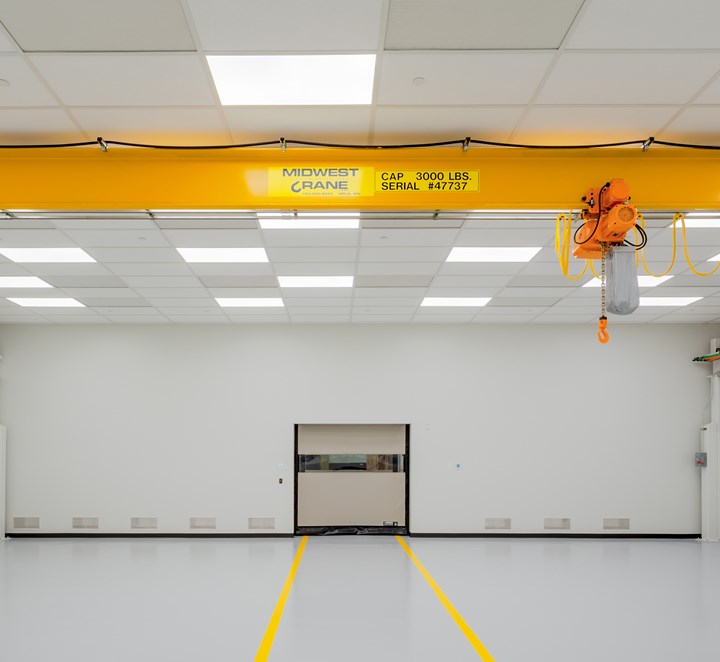
Spectrum Plastics Group has renovated its Minneapolis site, expanding its Class 8 cleanroom and injection molding capacity.
Photo Credit: Spectrum Plastics Group
Related Content
-
Medical and Molding Elite
When Jeff Smith received a notice evicting his promising 大象传媒 out of his house, it could have been the end of Elite Biomedical Solutions’ and Elite Precision Plastics’ stories before they really got started, instead it was just the beginning.
-
Allegheny Performance Plastics to Enter Health Care Sector
The custom molder has secured multiple projects in health care and will be adding cleanroom and white-room spaces, as well as injection molding machines, in support.
-
Consistent Shots for Consistent Shots
An integral supplier in the effort to fast-track COVID-19 vaccine deployment, Retractable Technologies turned to Arburg and its PressurePilot technology to help deliver more than 500 million syringes during the pandemic.