Nolato Group Acquires GW Plastics
The Vermont headquartered injection molding, moldmaking and contract manufacturing firm founded in 1955 becomes part of the global, publicly traded Swedish conglomerate.
The same year it marks its 65th anniversary, custom molder and moldmaker GW Plastics (Bethel, Vt.) has been acquired by the Nolato Group. Headquartered in Torekov, Sweden, Nolato has injection molding, blow molding and extrusion capabilities in thermoplastics and silicone, with customers in the healthcare, automotive, and consumer electronics industries. Nolato’s sales totaled $911 million in 2019.
GW Plastics, which has seven facilities globally and more than 1100 employees, has annual sales of approximately $207 million, according to Nolato, which acquired the company for approximately $230 million. The company has been privately held under the same ownership and leadership since 1983. The current management will remain with the company.
In a recorded conference call, Nolato CEO Christer Wahlquist said his company’s interest in GW was long running, and that GW’s strong North American presence would bolster an area of relative geographic weakness for Nolato, which is more represented in Europe and Asia.
GW’s facilities are located in Bethel and Royalton, Vt.; Grantham, N.H.; San Antonio, Tex.; Tucson, Az.; Querétaro, Mexico; Dongguan, China; and Sligo, Ireland. It has a total of nearly 540,000-ft2 of production space, including 12 medical cleanrooms. Nolato’s existing U.S. facilities are in Andover, N.J. (Nolato Jabar) and Baldwin, Mich. (Nolato Contour).
In the call, Wahlquist said GW is strong in scientific molding, with 85% of its 大象传媒 in pharma and medical devices, with 15% in automotive and general industry. Nolato is self described as “world leading in silicone injection molding.” It has capabilities in injection, blow molding (injection and extrusion), medical tube extrusion.
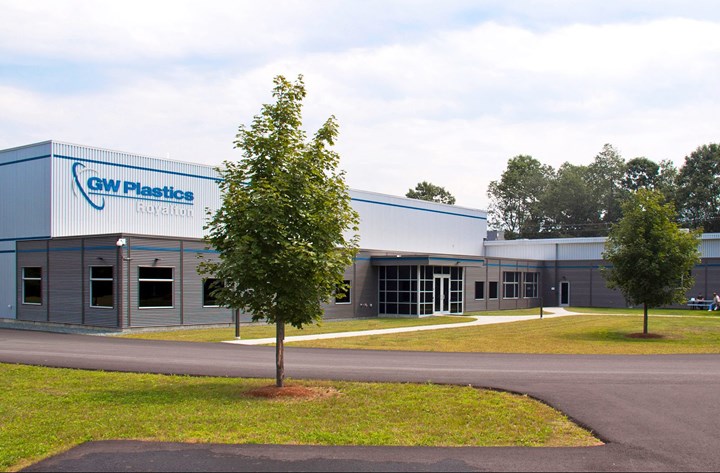
GW Plastics has been acquired by the Swedish plastics and silicone processor, Nolato.
Related Content
-
Get Color Changes Right In Extrusion Blow Molding
Follow these best practices to minimize loss of time, material and labor during color changes in molding containers from bottles to jerrycans. The authors explore what this means for each step of the process, from raw-material infeed to handling and reprocessing tails and trim.
-
Medical Molder, Moldmaker Embraces Continuous Improvement
True to the adjective in its name, Dynamic Group has been characterized by constant change, activity and progress over its nearly five decades as a medical molder and moldmaker.
-
What to Look for in High-Speed Automation for Pipette Production
Automation is a must-have for molders of pipettes. Make sure your supplier provides assurances of throughput and output, manpower utilization, floor space consumption and payback period.