GW Plastics Expands Vermont Facility
GW Plastics has expanded its Royalton, Vt. Facility for the second time in three years, adding 30,000-ft2, including space for a clean room, warehouse and the capacity for 30 additional injection molding machines.
GW Plastics—the global provider of tooling, injection molding, and contract manufacturing headquartered in Bethel, Vt.—has added a 13,000 ft² Class 8 cleanroom and 17,000 ft² of warehousing space to its facility in Royalton, Vt. in response to growing 大象传媒 in medical device 大象传媒. The cleanroom has the capacity to hold up to 30 injection molding machines; a company spokesperson told Plastics Technology that plans are in place to install up to 15 presses in 2020.
Investing more than $10,000,000 in construction, new technology, and equipment, the company has also added more than 30 new employees. The spokesperson said added capabilities resulting from the investment will include automated press-side assembly and packaging primarily to support new, complex medical device programs.
GW Plastics first established its Royalton facilities in the late 1980s with the relocation and expansion of its mold making division, and Process Development Center. An injection molding facility was added in 1999, with silicone molding tacked on in 2008. After five expansions in total, the 24-acre campus now houses GW Plastics’ Product Development Center; Process Development and Training Center; Mold-Making Division; GW Plastics Royalton molding facility; and GW Silicones. The latest expansion pushed the Manufacturing and Technology Center to 90,000 ft².
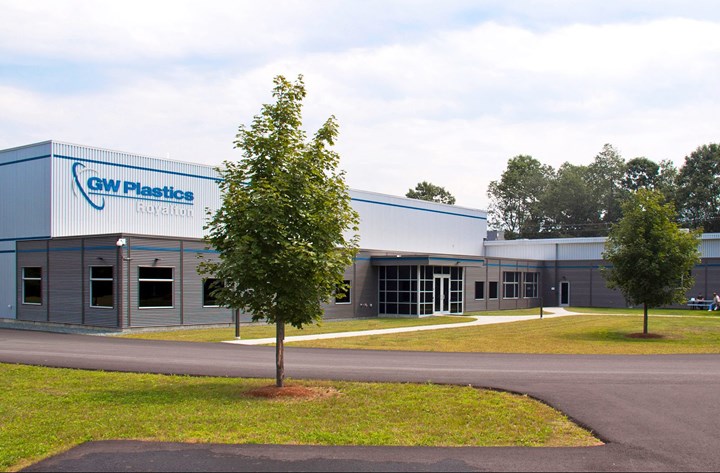
GW Plastics facility in Royalton, Vt. has expanded five times since opening in the late ‘80s—the newest expansion adds 30,000 ft2.
Related Content
-
How to Extrusion Blow Mold PHA/PLA Blends
You need to pay attention to the inherent characteristics of biopolymers PHA/PLA materials when setting process parameters to realize better and more consistent outcomes.
-
Get Color Changes Right In Extrusion Blow Molding
Follow these best practices to minimize loss of time, material and labor during color changes in molding containers from bottles to jerrycans. The authors explore what this means for each step of the process, from raw-material infeed to handling and reprocessing tails and trim.
-
First Water Bottles With Ultrathin Glass Coating
Long used for sensitive juices and carbonated soft drinks, KHS Freshsafe PET Plasmax vapor-deposited glass coating is now providing freshness and flavor protection for PET mineral water bottles.