Molder Pairs With Non-Profit to Ramp Up Fast Production of Affordable Ventilators
PMC SMART Solutions and Venti-Now Non-Profit worked together to determine the optimum product design and best assembly and testing processes to make production of as many as 1000 units/week as efficient as possible.

PMC helped determine the most efficient and repeatable assembly process for the Venti-Now ventilator.
In the face of the coronavirus pandemic, contract manufacturer PMC SMART Solutions LLC (Cincinnati) and Venti-Now Non-Profit Corp. (Cincinnati) worked to together to bring a new ventilator to market as quickly and inexpensively as possible. PMC’s president and CEO, Lisa Jennings, was introduced to the founders of Venti-Now as they sought a medical device manufacturer that could aid them in R&D.
Starting with a concept, design and early prototype for their emergency ventilator, PMC aided Venti-Now in design for manufacturability analyses to ultimately determine the optimum product design. The Venti-Now ventilator has a pneumatic/mechanical design, resulting in a small and portable device that is designed for quick production and maximum affordability. The Venti-Now uses standard, disposable BVM bags making it ideal for use in emergency situations in both hospital and field locations.
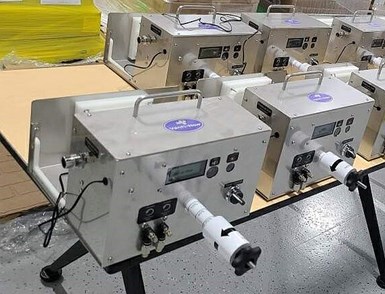
PMC supplied engineering, production, testing and documentation services for the Venti-Now ventilator.
At PMC’s manufacturing plant in Shelbyville, Ind., the company worked to standardize components to make ventilator for the lowest possible cost. PMC assessed supply chain and assembly options, that would make it possible to produce as many as 1000 units per week. Venti-Now utilized the full range of PMC’s capabilities, including product design and development, as well as strict adherence to FDA quality standards in production. PMC is FDA registered and ISO 13485 certified.
Related Content
-
Back to Basics on Mold Venting (Part 1)
Here’s what you need to know to improve the quality of your parts and to protect your molds.
-
Using Data to Pinpoint Cosmetic Defect Causes in Injection Molded Parts
Taking a step back and identifying the root cause of a cosmetic flaw can help molders focus on what corrective actions need to be taken.
-
Process Monitoring or Production Monitoring — Why Not Both?
Molders looking to both monitor an injection molding process effectively and manage production can definitely do both with tools available today, but the question is how best to tackle these twin challenges.