Mack Molding Adding Five New Injection Molding Machines
The three Cincinnati Milacron’s and two Wittmann Battenfeld’s, ranging in size from 1433 to 2500 tons, are destined for Mack’s Arlington, Vt. headquarters and Inman, S.C. facilities.
Custom plastic molder and contract manufacturer Mack Molding (Arlington, Vt.) is adding five new injection molding presses to its sites Arlington and Inman, S.C. Including the robots and infrastructure that will accompany the new machines, Mack is investing more than $5.5 million in the expansions.
The investments include two 1,433-ton Wittmann Battenfeld’s with 60-oz shot sizes in Arlington. Mack notes that one machine is already in place with the other expected to arrive in early summer. In Inman, Mack will install 1500-, 2000- and 2500-ton Cincinnati Milacron machines this fall. The 1500-ton press has a shot size of 362 oz, while the other two provide maximum shots 540 oz. Mack’s press fleet ranges in clamp force from 28 to 4000 tons, with shots from .6 to 800 oz. Included in that fleet are 21 presses that are 1400 tons or larger, making Mack one of the biggest non-automotive large-part molders in the U.S.
Jeff Somple, president, Mack Molding said the company made the normal power and water infrastructure investments required for presses of the size being added. In addition at the headquarters facility, Somple said a clean environment has also been built next to the first of the two new presses, since the part to be molded is used in the pharmaceutical space.
Somple also commented on the supply chain and delivery difficulties that have become standard these days. “Like everyone else,” Somple said, “we are seeing delivery delays and supply chain issues, especially in the electronics space.”
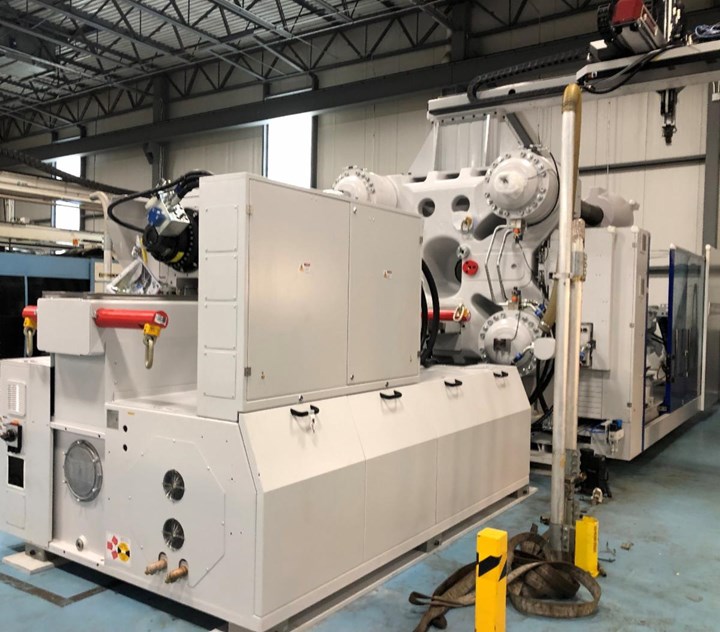
The first of two new 1433-ton Wittmann Battenfeld injection molding machines being installed at Mack’s headquarters in Arlington, Vt.
Photo Credit: Mack Molding
Related Content
-
Back to Basics on Mold Venting (Part 2: Shape, Dimensions, Details)
Here’s how to get the most out of your stationary mold vents.
-
Injection Molding: Focus on these Seven Areas to Set a Preventive Maintenance Schedule
Performing fundamental maintenance inspections frequently assures press longevity and process stability. Here’s a checklist to help you stay on top of seven key systems.
-
Three Key Decisions for an Optimal Ejection System
When determining the best ejection option for a tool, molders must consider the ejector’s surface area, location and style.