Mack Molding Names New VP of Manufacturing Operations
The Vermont headquartered custom injection molder and contract manufacturer named Rich Hornby as the new VP of manufacturing operations for its northern division.
Mack Molding (Arlington, Vt.) announced that Rich Hornby has been promoted to be the VP of manufacturing operations for Mack’s Northern Division. The custom plastic injection molder and supplier of contract manufacturing services noted that Hornby first joined the company in 2011 as a program manager focused on orthopedics and disposable medical devices. Since 2014, he has served as the headquarters plant manager. In a release, Mack Molding President Jeff Somple said Hornby’s tenure has been marked by significant program launches, team development and most recently tackling the myriad challenges posed by the pandemic.
In the new role, Somple said Hornby will unify Mack’s Vermont facilities, including implementing shared manufacturing platforms to boost productivity and product quality. As VP of Manufacturing Operations, Hornby will report directly to Somple and continue to lead Mack’s headquarters in Arlington, Vt., as well as taking responsibility for manufacturing operations in East Arlington and Cavendish, Vt. Additionally, he will be overseeing IT for Mack North.
Hornby draws on more than 20 years of service in the U.S. Air Force, from which he retired as a Lieutenant Colonel. In a release, Mack said this experience, his decade with Mack, and prior work as a program manager for Millstone Medical Outsourcing makes him a well-rounded leader. A graduate of the U.S. Air Force Academy, he earned an MBA from the Pennsylvania State University and a Six Sigma Green Belt Certification from Villanova University. Mack employs 1400 people across 11 facilities globally, including 660 staff in Vermont.
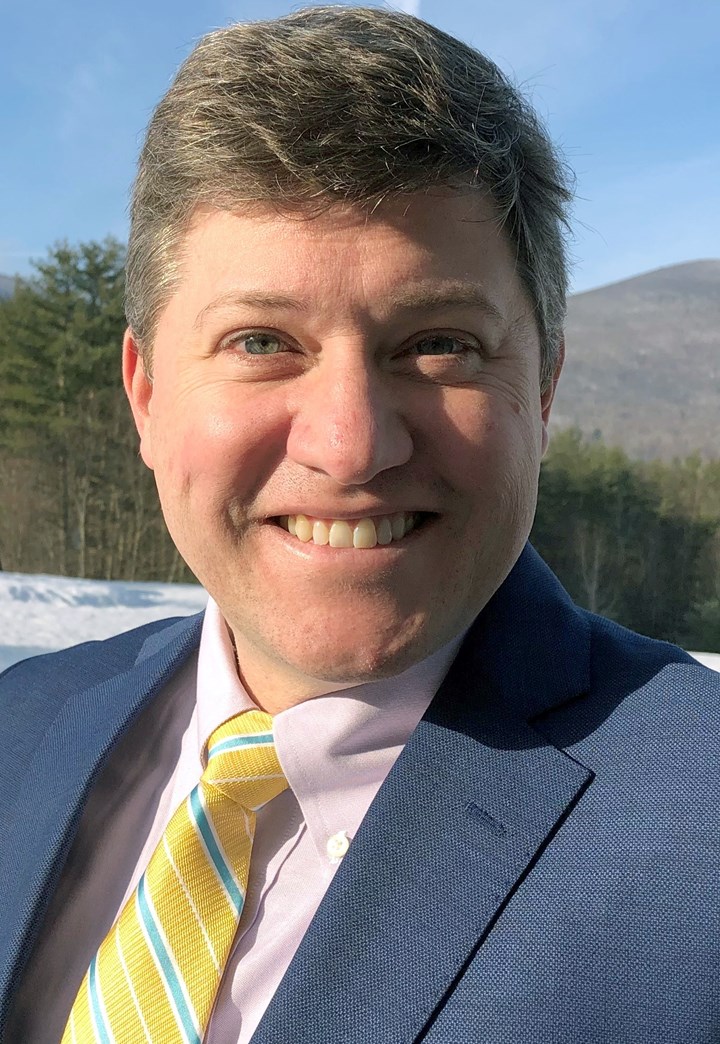
Rich Hornby has been promoted to VP of manufacturing operations for Mack Molding’s Northern Division.
Related Content
-
Is There a More Accurate Means to Calculate Tonnage?
Molders have long used the projected area of the parts and runner to guesstimate how much tonnage is required to mold a part without flash, but there’s a more precise methodology.
-
Got Streaks or Black Specs? Here’s How to Find and Fix Them
Determining the source of streaking or contamination in your molded parts is a critical step in perfecting your purging procedures ultimately saving you time and money.
-
A Systematic Approach to Process Development
The path to a no-baby-sitting injection molding process is paved with data and can be found by following certain steps.