Engel Introduces Pay Per Use Option
The company says the pay-per-use model allows its customers to make payments based on machine utilization.
Austrian injection molding machine and automation supplier Engel now offers its customers a pay-per-use model in addition to traditional machine purchases. Engel says that in addition to helping processors reduce their investment risk, this model can also boost production flexibility. An Engel spokesperson told Plastics Technology that the pay-per-use program will start in Europe and be available in North America soon.
Under this system, payment is based on machine utilization levels, with a unit price agreed to. This price can either be per unit molded or by machine operating time. Engel believes the pay-per-use model will help processors avoid the risk of binding up capital in a new machine or forcing them to seek approval for substantial investments. In either case, the procurement process can be concluded more quickly.
All production cells delivered under the pay-per-use model feature the online support and remote maintenance tool e鈥慶onnect.24 and are regularly maintained by Engel service technicians. In a service case, the Engel technicians can start maintenance work immediately, or it can be planned at an early stage to keep unavoidable machine downtime to a minimum. e鈥慶onnect.24 acquires the machine utilization as the basis for billing.
At the end of the agreed contract, the customer has the option of purchasing the machine, or Engel Used Machinery, the pre-owned machine company in the Engel Group, can take the machine back.
The financing partner backing the new pay-per-use solution by Engel is linx4 GmbH, which is headquartered in Vienna.
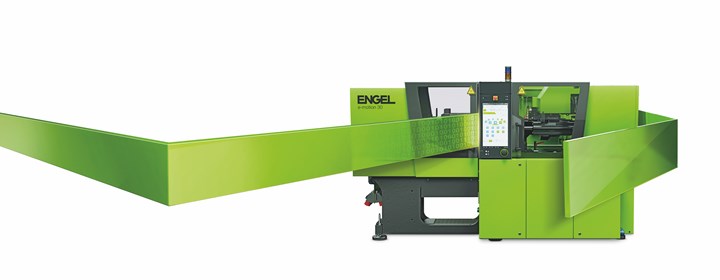
Engel says Pay per Use lets its customers reduce the investment risk of a new machine.
Photo Credit: Engel
Related Content
-
A Systematic Approach to Process Development
The path to a no-baby-sitting injection molding process is paved with data and can be found by following certain steps.
-
Understanding the Effect of Pressure Losses on Injection Molded Parts
The compressibility of plastics as a class of materials means the pressure punched into the machine control and the pressure the melt experiences at the end of fill within the mold will be very different. What does this difference mean for process consistency and part quality?
-
Got Streaks or Black Specs? Here’s How to Find and Fix Them
Determining the source of streaking or contamination in your molded parts is a critical step in perfecting your purging procedures ultimately saving you time and money.