Engel Achieves Record Earnings
For the fiscal year ending in March, the Austrian maker of injection molding machines and automation reported earnings of euro 1.7 billion ($1.86 billion), an all-time high.
Engel (Schwertberg, Austria) reported the highest turnover in the company’s history for the fiscal year 2022/2023, which ended in March. The company saw its turnover increase by 13%, generating revenue of euro 1.7 billion ($1.86 billion) compared to euro 1.5 billion in the year prior. The record year comes off an earnings period two years ago — fiscal year 2020/2021 — when sales had fallen 15% as the group generated revenue of euro 1.1 billion.
End-market wise, the automotive, medical, packaging and technical molding segments contributed to the record year. The company noted that in North America and Europe, machine investments were made to support continuing high demand for diabetes therapy products. Elsewhere, investments in logistics applications remained at a high level, according to the company, while the automotive industry has been the strongest driver of the company’s success over the last fiscal year, particularly in the Americas and Asia.
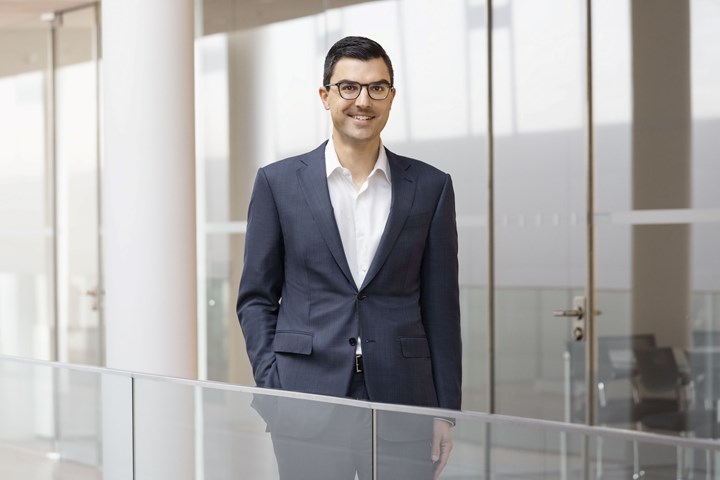
Stefan Engleder, CEO of the Engel Group, reported record annual earnings for the company in its most recent fiscal year.
Photo Credit: Engel
Related Content
-
A Systematic Approach to Process Development
The path to a no-baby-sitting injection molding process is paved with data and can be found by following certain steps.
-
Use These 7 Parameters to Unravel the Melt Temperature Mystery
Despite its integral role in a stable process and consistent parts, true melt temperature in injection molding can be an enigma. Learning more about these seven parameters may help you solve the puzzle.
-
Injection Molding: Focus on these Seven Areas to Set a Preventive Maintenance Schedule
Performing fundamental maintenance inspections frequently assures press longevity and process stability. Here’s a checklist to help you stay on top of seven key systems.