Change Over High-Output PET Blow/Fill/Cap Lines in Just One Week
Sidel delivered seven new PET bottle formats across two integrated water and soft-drink bottling lines within a week apiece.
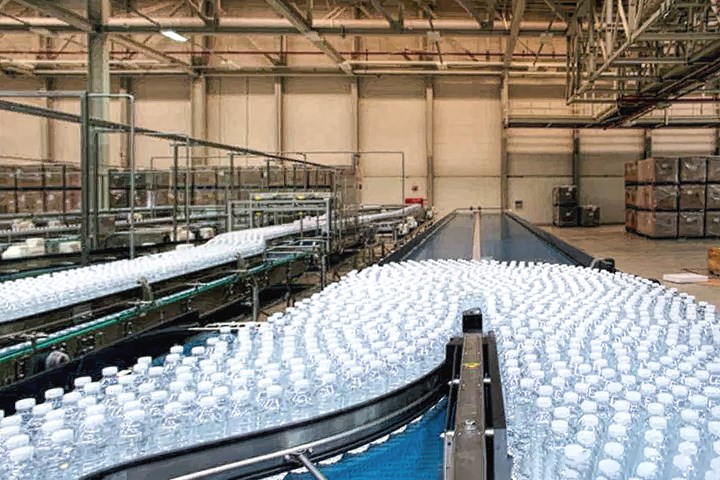
The MenaBev changeover of Sidel Combi integrated PET blow/fill/cap lines delivered an 11% boost in output for the still-water line, as well as a new 300-ml water bottle with 10% lighter weight. (Photo: Sidel)
MenaBev, based in Jeddah, Saudi Arabia, is said to be the leading bottler of water and soft drinks in the Middle East and North Africa. Its 300,000 m2 Mega plant near Jeddah is one of the largest and most automated PepsiCo bottling plants worldwide. It has three PET lines from Sidel – two for carbonated soft drinks and one for water – plus three can and glass lines.
Late last year, MenaBev needed to retool two Sidel Combi integrated PET blowing/filling/capping lines to produce, on one line, three new-look Aquafina water formats and, on the other line, four new “Carolina” bottle formats for PepsiCola. The Aquafina line involved new 330-ml, 500-ml and 1.5-liter bottles. For the 330-ml bottle, Sidel delivered a new design with 10% lighter weight.
Both Sidel Combi lines incorporate Universal stretch-blow molders, the one on the Aquafina line with 30 stations and the one on the Pepsi line with 24 stations. Each line was adapted to the new formats in one week apiece. What’s more, Sidel’s engineers were able to increase the Aquafina line’s output up to 60,000 bph from 54,000 bph previously. The Carolina Pepsi line maintained its optimized speed of 48,000 bph.
Related Content
-
Get Color Changes Right In Extrusion Blow Molding
Follow these best practices to minimize loss of time, material and labor during color changes in molding containers from bottles to jerrycans. The authors explore what this means for each step of the process, from raw-material infeed to handling and reprocessing tails and trim.
-
A Purge Solution for the Blow Molding and Compounding Industries
New commercial purge compounds for new industries from Chem-Trend.
-
PolyJohn Turns to Blow Molding, Doubles Its Productivity
Leading maker of portable sanitation products knew thermoforming, sheet extrusion, rotomolding and injection molding. Then it found the missing link to higher productivity and new markets: blow molding.