Bosch Rexroth Moving to Larger Charlotte Facility
Bosch Rexroth will move its factory automation technology manufacturing into a “factory of the future” by summer 2024.
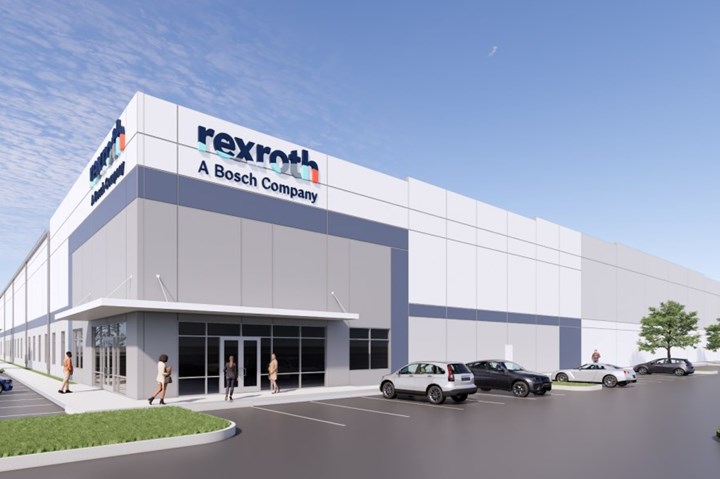
Responding to growth in its factory automation 大象传媒, Bosch Rexroth is moving to a new, larger plant that will be built to order as “a showcase environment of what a factory of the future can be today.” (Photo: Bosch Rexroth)
is moving and expanding while remaining in Charlotte, N.C., its home for over 30 years. The company’s linear and assembly technology manufacturing will occupy a custom-built plant at 409 Tyvola Rd., about 8 miles from the South Lakes Drive location it has occupied for 26 years. The new facility will have a total footprint of 227,500 ft2, expanding Bosch Rexroth’s manufacturing space by over 25%, with additional room for future expansion. Approximately 200,000 ft2 of the new space will be dedicated to lean manufacturing and logistics, and the rest will include a customer showroom and innovation center, training facilities, collaboration space, offices, and multi-purpose galleria. The new building will have plenty of space for R&D, the company says, and will “be the ideal representation of what truly means to be a factory of the future.”
Bosch Rexroth supplies hydraulics, electric drive and control technology, gear technology and linear motion and assembly technology, including software and interfaces for the Internet of Things (Industry 4.0).
Related Content
-
Why ‘Smart’ Blending May Be Right for You
Industry 4.0 smart controllers dial in the right recipes quickly with gain-in-weight blenders to eliminate material waste, cost overruns.
-
Golf Equipment Manufacturer Scores Higher Productivity With Automated Cell
Ping was able to reduce labor and waste at its production facility in Phoenix via an automated molding cell courtesy of Wittmann.
-
Pursuing Paperless: Injection Molders Who Have Embraced Digitization
Read about injection molders who have shifted everything from quality control and scheduling to production and process monitoring to the digital realm.