Extrusion: Solving Surging in Two-Stage Screws
This usually crops up when the two stages are not matched in output. The best solution is to install a pressure-adjusting valve at the discharge end of the extruder.
Ever had a two-stage screw that is unstable all of the time, regardless of temperature settings and screw speed? It happens when the two stages are not matched to the polymer output and die backpressure.
A two-stage screw is basically two separate screws that must work in tandem. The first stage of the screw feeds and melts polymer before dumping it into the vent area. The second stage of the screw takes the melted polymer from the vent, pressurizes it, then pumps it through a die. The outputs of the two stages need to be relatively well balanced or else constant instability will develop that can’t be solved by adjusting the operating conditions.
This situation has been known to happen when a two-stage screw designed for a specific polymer is used to run a different polymer. The result is a reduction in the volumetric output of the first stage. This leaves the second stage too deep for the output of the first stage, and consequently the length of fill is altered. When designing a new two-stage screw with a good estimate for the head pressure, the fill length can be calculated by manipulating the depths to balance the drag flow and pressure flow to obtain a reasonably stable length of fill. But when the polymer being processed is changed, the optimum fill length may be irreversibly lost.
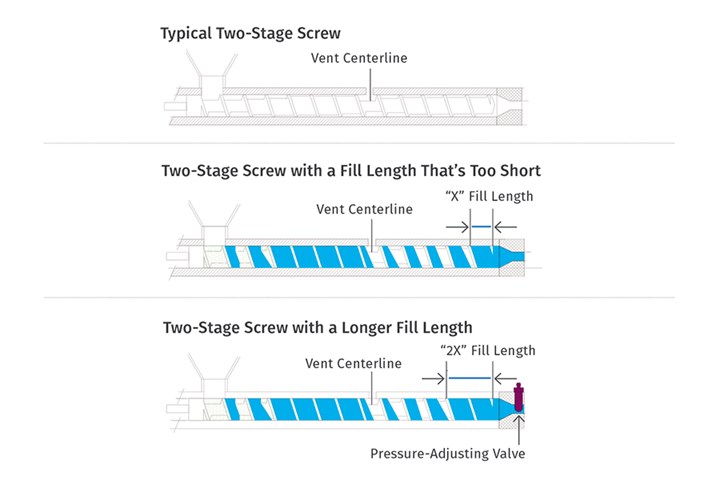
In order for the second stage of the screw to be stable it must have a minimum length of fill so that pressure flow is a small percentage of the drag flow. Otherwise, it will continuously vary in fill length, which changes its output. As the fill length increases, the output of the second stage increases. As the fill length decreases, the output of the second stage decreases. So, when the two stages are not matched in output against a particular head pressure, the second stage can continuously vary in fill length. This results in surging. The surge will not be very noticeable in the power draw because most of the power is used in the first stage for melting, with much less used in the second stage for melt conveying.
For such situations, the best solution is to install a flow-control valve at the discharge of the extruder and increase the backpressure until the cycling stops, indicating enough fill to develop a stable condition. Alternatively, you might be able to solve this problem by adding filter screens or switching to a more restrictive breaker plate, but that’s not easily adjustable and can require continuous retrofitting if the polymers or even bulk densities are constantly changing. The accompanying illustration shows the typical two-stage screw, compared with a two-stage screw with too short a fill length and the screw with a flow-control valve to provide control over the fill length regardless of the output from the first stage.
I’ve seen this problem crop up more frequently of late because extruders are adding higher percentages of recycled material to this process. The reduced bulk density of the recycled material decreases the specific output of extruders; a two-stage screw that worked well when there was little or no regrind/recycle is now unstable. A new screw design could correct this, but then you are still not ready for the next polymer or a different bulk density.
ABOUT THE AUTHOR: Jim Frankland is a mechanical engineer who has been involved in all types of extrusion processing for more than 40 years. He is now president of Frankland Plastics Consulting, LLC. Contact jim.frankland@comcast.net or (724) 651-9196.
Related Content
Understanding Melting in Single-Screw Extruders
You can better visualize the melting process by “flipping” the observation point so the barrel appears to be turning clockwise around a stationary screw.
Read MoreRoll Cooling: Understand the Three Heat-Transfer Processes
Designing cooling rolls is complex, tedious and requires a lot of inputs. Getting it wrong may have a dramatic impact on productivity.
Read MoreThe Importance of Barrel Heat and Melt Temperature
Barrel temperature may impact melting in the case of very small extruders running very slowly. Otherwise, melting is mainly the result of shear heating of the polymer.
Read MoreThe Role Barrel Temperatures Play in Melting
You need to understand the basics of how plastic melts in an extruder to properly set your process and troubleshoot any issues. Hint: it’s not about the barrel temperature settings.
Read MoreRead Next
Lead the Conversation, Change the Conversation
Coverage of single-use plastics can be both misleading and demoralizing. Here are 10 tips for changing the perception of the plastics industry at your company and in your community.
Read MoreFor PLASTICS' CEO Seaholm, NPE to Shine Light on Sustainability Successes
With advocacy, communication and sustainability as three main pillars, Seaholm leads a trade association to NPE that ‘is more active today than we have ever been.’
Read MorePeople 4.0 – How to Get Buy-In from Your Staff for Industry 4.0 Systems
Implementing a production monitoring system as the foundation of a ‘smart factory’ is about integrating people with new technology as much as it is about integrating machines and computers. Here are tips from a company that has gone through the process.
Read More