Extrusion: Evaluating Screw Design for Multi-Material Recycling
Since many plastic products are made of a combination of materials with very different melting points, careful consideration must be given to designing screws when it comes time to recycle these products.
Today, with all the focus on recycling, some thought must be applied to avoid processing issues when recycling coextruded or co-injection molded parts. Many plastic products are composed of several different polymer layers to provide special properties such as barrier, gloss, color, wear, etc. that are very thin but have to be considered when designing screws for recycling. This is particularly true for semi-crystalline polymers.
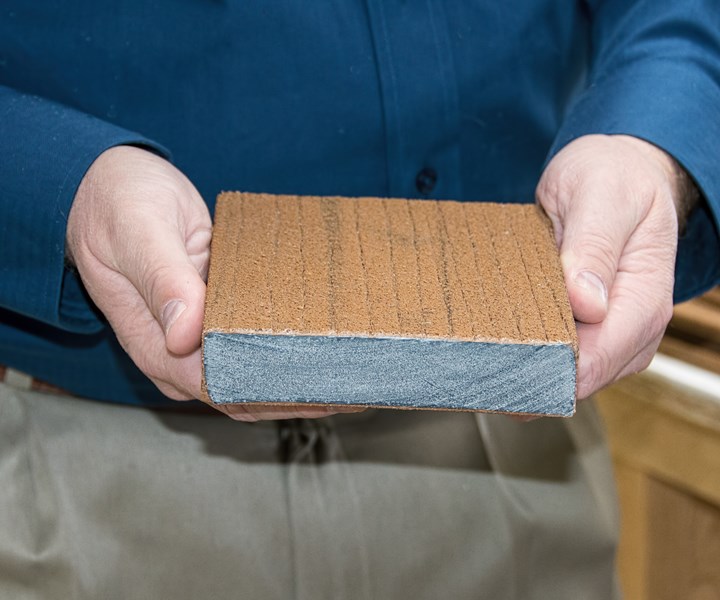
Screw design must be considered carefully when recycling products composed of combinations of materials. (Shown here: coextruded deck board with a core layer of mineral-filled post-industrial HDPE and colored HDPE capstock, made by N.E.W. Plastics Corp.)
Semi-crystalline polymers do not soften at all until very near their melting point. For example, let’s consider a part made from a semi-crystalline polymer such as HDPE with an additional semi-crystalline layer such as PET co-extruded or overmolded. In that case, the HDPE melts at 266 F and the PET at 500 F. Since the bulk of the recycled article, say more than 90%, is HDPE, its normal processing temperature is typically in the range of 370-400 F. PET would not even begin to soften—let alone melt—at that temperature. To somehow get the overall processing temperature up to where the PET could also melt would degrade or burn the HDPE. The reverse issue also applies: If the main polymer were PET, the required processing temperature would heavily degrade the HDPE.
Semi-crystalline polymers do not soften at all until very near their melting point.
There is a little less concern when recycling parts made of amorphous polymer layers, or combinations of amorphous polymers, as they typically soften and become rubbery well below their typical processing temperatures. Consequently, there can be quite a disparity between their normal processing temperatures and the ability to pass them through any tight clearances in the screw. Their softening point is referred to as the glass-transition temperature, or Tg. However, even with amorphous polymers there is a limit to how far apart the Tg can be for each polymer so as not to plug the screw. Semi-crystalline polymers also have a Tg—they are called semi-crystalline because they contain a portion of amorphous polymer. Generally, though, it does not affect the flow to a large enough degree, and they can be considered not flowable until the melting point. Hence the melting point applies to semi-crystalline polymers more than the Tg for the purposes of this discussion.
In recycling coextruded or co-injected parts having crystalline polymer layers, the use of barrier screws and shear-type mixers (such as the many varieties of Maddock-style mixers) must be carefully evaluated. If one of the layers is a semi-crystalline polymer with a much higher melting point than the normal processing temperature of the main polymer, it will be trapped behind the tight clearances of the barrier flight and the mixer lands. The higher-melting semi-crystalline resin will simply not break down and flow over the barrier flight and or the shear clearances in any mixers. Even a relatively low percentage (less than 5%) of the higher-melting polymer will plug the screw, causing unstable and reduced output.
For any recycled material, including films, attention must be paid to the melting and or relative softening points of the component polymers to determine whether the screw design is suitable for that combination of polymers. If there is a thermal incompatibility, then the use of barrier screws and restrictive mixing devices must be carefully evaluated, and the screw design based around melting without such devices. This will typically limit the potential output, so it needs to enter into the original estimation for profitability of processing recycle. Other types of screw without tight clearances will allow the higher-melting or higher-Tg materials to simply pass through the screw like an inert filler.
ABOUT THE AUTHOR: Jim Frankland is a mechanical engineer who has been involved in all types of extrusion processing for more than 40 years. He is now president of Frankland Plastics Consulting, LLC. Contact jim.frankland@comcast.net or (724) 651-9196.
Related Content
Is a Gear Pump Right for Your Single-Screw Operation
As with everything else, there are pros and cons, but more of the former. They provide processors higher rates while decreasing the temperature of the extrudate while enabling downgauging.
Read MoreUnderstanding Melting in Single-Screw Extruders
You can better visualize the melting process by “flipping” the observation point so the barrel appears to be turning clockwise around a stationary screw.
Read MoreChoosing the Right Gearbox and Motor for Your Single-Screw Extruder
Extruder OEMs are typically very good at sizing motors and gear boxes for extrusion applications. But you have the final decision on the acceptance of the design. Here’s what you should consider.
Read MoreUnderstanding the Incumbent Resin Effect
When you are looking to replace an existing resin with a new one, in trials sometimes the “incumbent” resin will cause gels and other defects. Here’s what to look for.
Read MoreRead Next
Making the Circular Economy a Reality
Driven by brand owner demands and new worldwide legislation, the entire supply chain is working toward the shift to circularity, with some evidence the circular economy has already begun.
Read MoreFor PLASTICS' CEO Seaholm, NPE to Shine Light on Sustainability Successes
With advocacy, communication and sustainability as three main pillars, Seaholm leads a trade association to NPE that ‘is more active today than we have ever been.’
Read MorePeople 4.0 – How to Get Buy-In from Your Staff for Industry 4.0 Systems
Implementing a production monitoring system as the foundation of a ‘smart factory’ is about integrating people with new technology as much as it is about integrating machines and computers. Here are tips from a company that has gone through the process.
Read More