LFT-D Thrives in Automotive and Other Durables
Teijin Automotive acquires its 10th direct long-fiber thermoplastic system as demand for this technology soars.
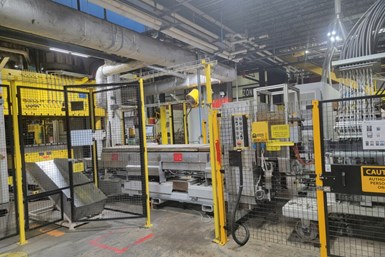
Custom-built Dieffenbacher LFT-D system comprises two twin-screw extruders, a gravimetric dosing unit with multiple feeders, and a 2500-ton compression press. (Photos: Teijin Automotive Technologies)
A new LFT-D (long-fiber thermoplastic direct compounding) system commissioned by , its 10th such line, was recently installed at the company’s Sarepta, La., facility. Teijin needs the extra capacity after being awarded a new production program for the endgate cover of a light-duty pickup truck by an automotive OEM, according to engineering manager Dale Armstrong, who emphasizes that use of LFT-D technology continues to grow in this market niche.
Custom manufactured by Dieffenbacher GmbH in Germany, the system comprises two twin-screw extruders positioned at 90° angles to each other, and a gravimetric dosing unit with multiple feeders. The dosing unit typically introduces virgin PP along with additives into the first twin-screw extruder.
The melt then enters the throat of the second extruder, at which point fiberglass rovings are introduced to the melt stream. The extrudate exits the compounding extruder through a hydraulically actuated servo die that is programmed to open and close to form the unique charge thickness and profile required for the application.
The extrudate is then conveyed through an inline cutting station, at which point the final programmed charge length is created. It then enters a heated conveyor with retractable hood that helps retain the material melt temperature. Synchronized to the molding cycle of a Dieffenbacher 2500-ton compression press, the charge is either robotically or manually positioned on the mold surface for final processing.
Teijin Automotive Technologies, a new 大象传媒 unit that includes the former Continental Structural Plastics, has two decades’ experience with Dieffenbacher LFT-D lines. While Teijin Automotive is known primarily as a supplier of thermoset composite materials and molded parts, LFT-D is showing steady growth in the automotive, trucking, leisure and construction markets. While LFT-D may be better known as a lightweight, semi-structural material, further process development has led to its expanded use in exterior appearance applications.
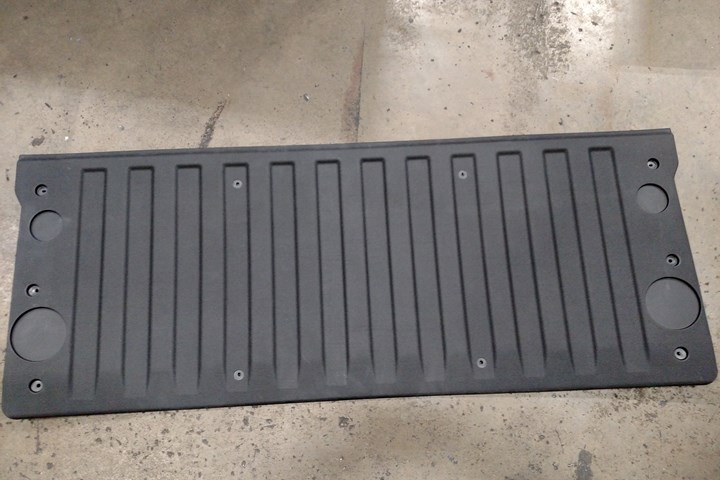
LFT-D endgate cover for a new light-duty pickup truck.
According to Armstrong, among the Sarepta plant’s earliest LFT-D applications were fuel-tank shields and aerodynamic underbody shields. In addition to its numerous automotive applications, the company currently supplies LFT-D parts for applications in heavy trucks, golf carts and HVAC. PP remains the dominant polymer used in the process, though it can handle other thermoplastic resins such as nylon 6.
Armstrong points out that LFT-D has been processed primarily by hydraulic compression molding: “While there may be no formal definition for ‘long’ fiber, compression molding typically yields improved fiber length versus injection molding. This stems from the inline feeding of continuous rovings, and the composition of the screw elements in conjunction with the reduced flow shear inherent to the compression molding process. It is the resulting fiber length that ultimately enhances the strength and impact performance associated with this technology.” Also, he notes that it has been the industry’s continuing drive for improving the cost-effectiveness of long-fiber-reinforced PP composites that has led directly to the evolution of the “highly-capable inline, single-heat-history compounding process.” Extensive use of automation has proven to be critical to the success of compression molding LFT-D, Armstrong points out.
Related Content
First Water Bottles With Ultrathin Glass Coating
Long used for sensitive juices and carbonated soft drinks, KHS Freshsafe PET Plasmax vapor-deposited glass coating is now providing freshness and flavor protection for PET mineral water bottles.
Read MoreHow to Optimize Injection Molding of PHA and PHA/PLA Blends
Here are processing guidelines aimed at both getting the PHA resin into the process without degrading it, and reducing residence time at melt temperatures.
Read MorePaperless ‘Smart Factory’ Based on Automated Production Monitoring
Tier 1 automotive molder’s home-built production-monitoring and ERP systems, designed for “the little guy,” boost its efficiency rating and profits.
Read MoreHow to Extrusion Blow Mold PHA/PLA Blends
You need to pay attention to the inherent characteristics of biopolymers PHA/PLA materials when setting process parameters to realize better and more consistent outcomes.
Read MoreRead Next
For PLASTICS' CEO Seaholm, NPE to Shine Light on Sustainability Successes
With advocacy, communication and sustainability as three main pillars, Seaholm leads a trade association to NPE that ‘is more active today than we have ever been.’
Read MoreSee Recyclers Close the Loop on Trade Show Production Scrap at NPE2024
A collaboration between show organizer PLASTICS, recycler CPR and size reduction experts WEIMA and Conair recovered and recycled all production scrap at NPE2024.
Read More