iMFLUX Plots Path to Autonomous Molding
iMFLUX used a virtual event in May to lay out a path to autonomous molding where “the machine is making intelligent decisions on behalf of the operator.”
On May 26, injection molding technology supplier iMFLUX described the company’s “journey to autonomous molding” in the first of its virtual Fearless Innovation Series, partnering on this broadcast with Absolute Haitian, the exclusive distributor of Haitian injection molding machines in the U.S. and Canada. Absolute Haitian and iMFLUX announced an agreement in April to integrate iMFLUX processing software as an option on Haitian servo-hydraulic and Zhafir electric injection molding machines. iMFLUX applies constant low-pressure injection to ensure uniform filling and packing with faster cycles, more uniform quality, and the ability to adapt in real time as conditions vary.
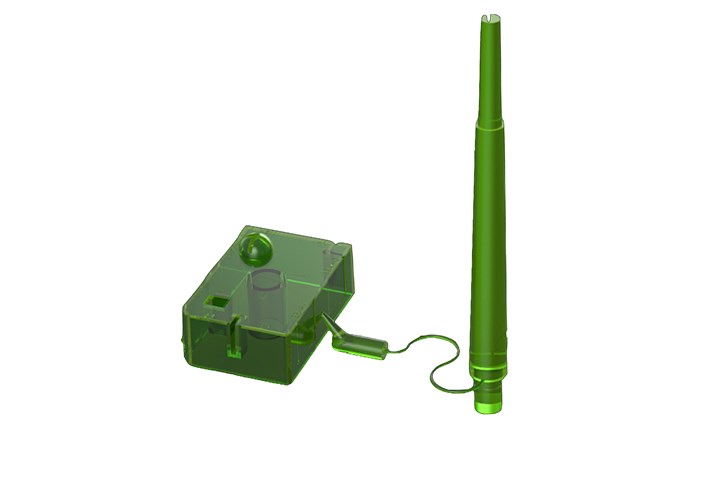
The iMFLUX low-pressure process “breaks the rules,” such as molding thick-to-thin-to-thick in this PP demo part.
In a discussion of the company’s “innovation pipeline,” Gene Altonen, iMFLUX chief technology officer, detailed iMFLUX’s current technologies and how they will be augmented going forward toward the ultimate goal of autonomous molding. The current capabilities covered by Altonen included auto-tuning; auto-viscosity adjust (AVA); Smart Start 1.0, whereby molders can “script” shot parameters for startup; integration of iMFLUX’s process into simulation software; “Process Fingerprinting,” wherein the system creates a unique pressure-profile “fingerprint” that can be moved from press to press; and rethinking tooling so that it takes advantage of iMFLUX’s unique process (e.g., lower pressure means cooling channels can be closer to the mold surface).
What’s Next?
Altonen then shifted his discussion to what’s currently in development at iMFLUX, starting with Smart Start 2.0. Once the optimum velocity profile is determined, based on low constant pressure to eliminate startup scrap with a dyanmic startup solution. As its name indicates, Quick Process will speed the creation of an optimized processing window. The first shot determines the minimum pressure and time needed to fill the part. The second shot then finds the processing window for good parts; and the third shot fully develops the process. Thus, in three cycles, Altonen said, an optimized window can be found, versus undertaking a more involved design of experiments (DOE) or other method to find a part’s processing window.
iMFLUX has a much less complex relationship than conventional molding between variables like transfer position, injection velocity, etc.
Along similar lines, Auto Process Development automates that procedure, with the press able to determine the optimum process window. Altonen said this is possible because iMFLUX has a much less complex relationship than conventional molding between primary control variables like transfer position, injection velocity and holding pressure.
DataFLUX is a planned update that allows data acquisition, analysis and correlation, and the creation of what iMFLUX calls novel control parameters. Altonen said this would serve as a building block for machine learning and what ultimately becomes autonomous molding. DataFLUX is a data-acquisition system that makes creation of novel process parameters possible. These can be calculated offline and measured in real time.
Altonen concluded with a description of Autonomous 2.0, iMLUX’s vision of the future of molding where machine-learning algorithms pair with DataFLUX’s novel control parameters to allow real-time intelligent control. “Where we’re headed is taking all that info from dataFLUX and creating machine-learning algorithms,” Altonen said, noting that the company is already doing this at some level in its R&D labs. “It’s a journey, and this would be out there towards the end of the journey, but we’ve made great progress and are super-excited about future that this holds.”
Related Content
NPE2024 Wrap-Up: Sustainability Dominates Show Floor News
Across all process types, sustainability was a big theme at NPE2024. But there was plenty to see in automation and artificial intelligence as well.
Read MoreReal-Time Production Monitoring as Automation
As an injection molder, Windmill Plastics sought an economical production monitoring system that could help it keep tabs on its shop floor. It’s now selling the “very focused” digital supervisor it created, automating many formerly manual tasks.
Read MorePolyJohn Turns to Blow Molding, Doubles Its Productivity
Leading maker of portable sanitation products knew thermoforming, sheet extrusion, rotomolding and injection molding. Then it found the missing link to higher productivity and new markets: blow molding.
Read MorePaperless ‘Smart Factory’ Based on Automated Production Monitoring
Tier 1 automotive molder’s home-built production-monitoring and ERP systems, designed for “the little guy,” boost its efficiency rating and profits.
Read MoreRead Next
Moving Toward ‘Autonomous Molding’ with a Uniform-Low-Pressure Process
A new low-pressure injection molding process has aroused interest among molders and machine suppliers. In his second article on iMFLUX, the inventor of the process explains how it is evolving to support the overall industry goal of self-correcting molding processes that can compensate for common causes of variation to maintain consistent part quality.
Read MoreAbsolute Haitian and iMFLUX Partner
The distributor of Haitian injection molding machines in the U.S. and Canada has partnered with the P&G subsidiary to bring iMFLUX’s low constant-pressure molding platform to the market.
Read More