‘World First’ 3D Printing Material for Wear Parts
Liquid DLP resin makes high-precision parts with wear life 30 to 60 times longer than conventional 3D printed parts.
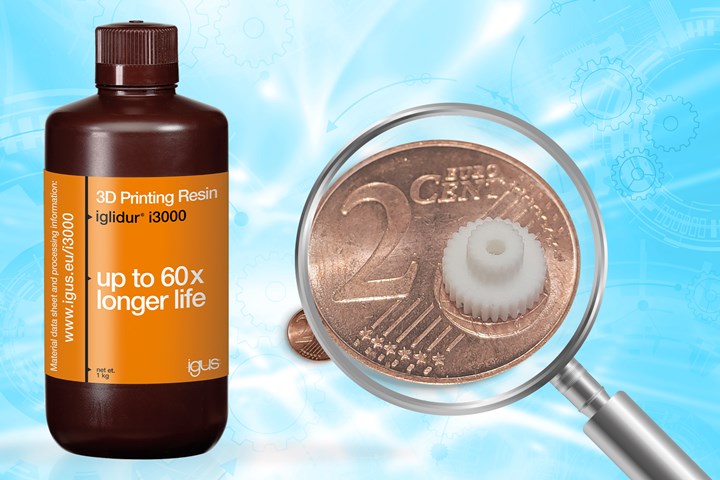
In addition to its new iglidur i3000 DLP resin, igus offers custom printing services that now includes DLP capability with resolution down to 0.035 mm. (Photo: igus)
What’s said to be the first 3D printing material for highly wear-resistant moving mechanical parts has been introduced by of Germany. Its new iglidur i3000 proprietary liquid resin is said to enable additive manufacturing by digital light processing (DLP) of very small, precise components in the millimeter range with wear life 30 to 60 times longer than conventional 3D printing resins.
The company says DLP is particularly suitable for printing tiny parts with high precision, such as gears with tips just 0.3 mm thick. The tips also have very smooth surfaces that require no post-treatment, igus says. The new material, like others from igus, contains solid microscopic lubricant particles and needs no external lubrication.
In addition to the new material, igus also offers custom-printed components. Up to now, igus offered 3D printing by selective laser sintering (SLS) and fused deposition modeling (FDM). Now, igus is expanding its 3D printing service with DLP printers that can achieve a resolution of just 0.035 mm. It offers an online tool with which customers can upload STEP files for their components or configure gears in just a few clicks.
Related Content
-
5 Trends in 3D Printed Injection Mold Tooling
3D printing has moved beyond conformal cooling, and is now being applied to injection molds more broadly. Observations on additively manufactured mold tooling from the Plastics Technology Expo — PTXPO 2025.
-
Make Every Shot Count: Mold Simulation Maximizes Functional Parts From Printed Tooling
If a printed tool only has a finite number of shots in it, why waste any of them on process development?
-
Insight Polymers & Compounding Unveils New Conductive Products Line
The new conductive products line will also be produced for injection molding and extrusion.