Ultrasonic Inserts and Heat Staking Kits for Thermoplastics
Made from brass with inch or metric threads, the E-Z Sonic inserts in E-Z Lok’s threaded insert assortment kits can be installed via ultrasonic horn or heat driver.
Share
Read Next
Molded-In Threaded Inserts: The Basics
Molded-In Threaded Inserts: The Basics
— a manufacturer and distributor of threaded inserts for metal, plastic and wood — is now offering E-Z Sonic threaded insert assortment kits. Designed for post-molding installation in thermoplastics such as acrylic, polypropylene and PVC, E-Z Sonic inserts are machined from brass and available with both inch and metric threads.
The tapered and straight designs can be installed with an ultrasonic horn or a heat driver. E-Z Lok says product benefits include high torque and pullout resistance via straight, single- and double-vane designs in flush or flanged configurations. Each kit includes 200 inserts and five installation tips for use with a soldering iron.
Straight inserts provide superior torque and pullout resistance, while enabling thinner boss walls. Flush inserts enable installation even with or below the material surface. Flanged inserts are well suited for electrical connections or for additional pullout resistance in reverse installations.
E-Z Sonic straight threaded ultrasonic inserts feature a lead-in pilot to facilitate installation. Machined out of brass, the inserts are available with internal threads from 2 to 3/8 in. and 2.5 to 6 mm. In addition to post-molding installation in thermoplastics, the heat staking threaded insert assortment kits can also add machine threads to 3D printed parts and prototypes.
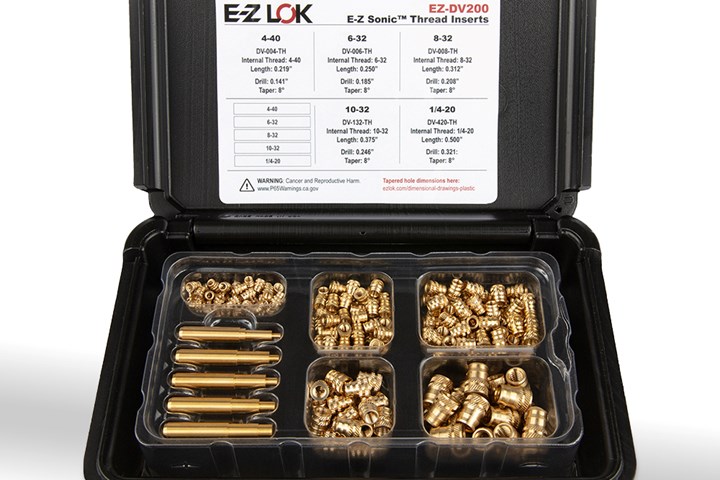
E-Z Lok’s E-Z Sonic insert kits feature 200 inserts and five installation tips for use with a soldering iron. Photo Credit: E-Z Lok