Thermoforming Equipment Supplier Expands Virtual Services
Illig has expanded its customer service program with augmented reality devices and software solutions.
Manufacturer of thermoforming and packaging systems (U.S. office in Indianapolis) has expanded its customer service program with new virtual tools. Augmented reality (AR) devices and software solutions have been deployed to support customers remotely. The complementary visualization technologies enables the use of technical maintenance, machine health checks, as well as the execution of a variety of tests in the Illig Technology Center (ITC) in real time. Pandemic-related lockdowns and restrictions on global travel have accelerated the acceptance of expanded remote technical customer support.
Factory acceptance tests (FAT) and subsequent machine commissioning at the customer's site are usually carried out with the physical presence of Illig technicians and customer staff. Illig has offered the possibility to carry out these demanding and complex procedures online for years. Until now, the direct exchange took place via portable devices such as smartphones, tablets, and high-end cameras in real time.
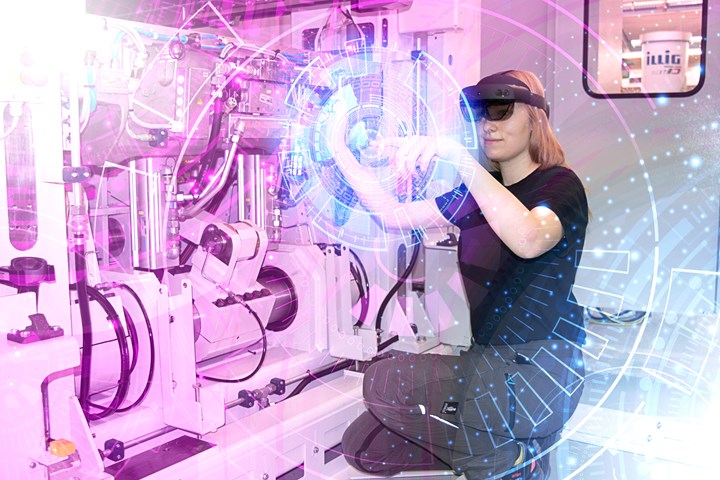
Virtual services extends and facilitates communication in the commissioning process and speeds up execution of related tasks. With AR technology, Illig has expanded its digital service offering with the help of Microsoft HoloLens2. These mixed reality glasses allow the user to display interactive 3D projections in the immediate environment. Adapted to Illig's requirements, the glasses can be used, for example, for tests in the ITC with direct transmission to the customer. Customers can actively participate in real time from their location using Microsoft TEAMS via smartphone, tablet or PC. Other applications with this technology include FATs, customer training, and live product presentations.
Additional options for accessible live communication for ad hoc support includes the use of the Inosoft i40 software portal at Illig. This web-based real-time support enables simple and fast direct contact with the customer via moving image and sound without the customer having to install any special software.
Related Content
-
A Processor's Perspective: What's Driving Growth in Heavy-Gauge Thermoforming
Key factors for the progress are innovative materials, advanced automation and precision engineering.
-
Collaboration Key to Development of Thermoformed EV Charging Stations
Heavy-gauge former Ray Products and custom sheet extruder Sekisui Kydex combine expertise in materials science and processing to commercialize cost-effective charging units.
-
Cobot Creates 'Cell Manufacturing Dream' for Thermoformer
Kal Plastics deploys Universal Robot trimming cobot for a fraction of the cost and lead time of a CNC machine, cuts trimming time nearly in half and reduces late shipments to under 1% — all while improving employee safety and growth opportunities.