System Simplifies Thread-Repair Insert Installation
NPE2024: C-Sert Manufacturing’s new installation system is designed to speed up the removal of damaged threads and the creation of a new pilot hole — 10 to 15 minutes per hole — with just four components.
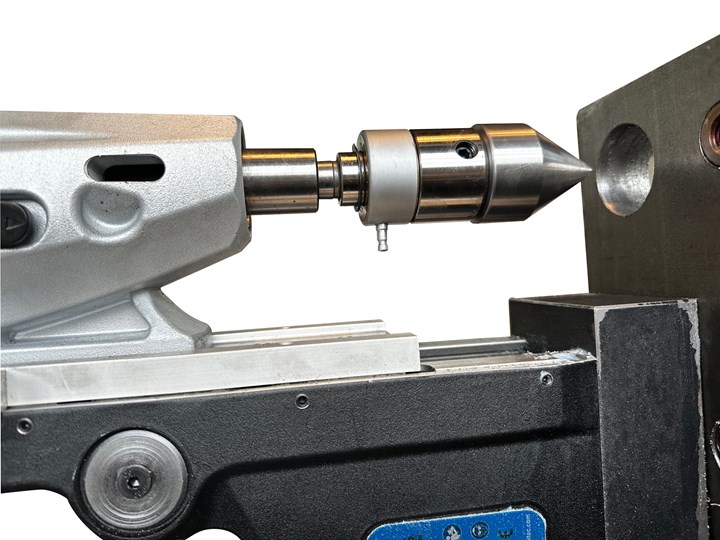
C-Sert’s installation system utilizes a 60-degree center to position the mag drill squarely on the platen hole. Source: C-Sert
C-Sert Manufacturing is introducing a new installation system for its C-sert thread-repair inserts, enabling fast, safe installation on injection molding machine platens. C-Serts are self-tapping inserts made from through-hardened S7 high-impact tool steel for the permanent repair of damaged platen holes, where frequent mold changes and production pressures can lead to stripped threads. C-Serts enable a permanent repair that’s guaranteed for the life of the press against thread wear, pullout and back-out. Self-tapping and self-aligning, C-Serts are designed to install straight.
The new C-Sert installation system can remove damaged threads and create new pilot holes in 10 to 15 minutes per hole. The system consists of four components, starting with a 29-lb German-made magnetic drill. Enabling one-person operation, C-Sert says the drill prevents injuries, minimizes downtime and eliminates the need for 100-lb magnetic drills or overhead cranes.
Next, annular cutters replace traditional drill bits, creating far lower tool pressure so the 29-lb mag drill can open large holes up to 1 ¾ inch. A 60-degree center positions the mag drill squarely on the platen hole, preventing misaligned drilling or drill placement, and the paste coolant replaces a mag drill’s traditional, gravity-fed coolant system. C-Sert says a teaspoon of the paste goes into the hollow annular cutter and melts as the cutter heats up, keeping the coolant on the cutting surface. The company notes that traditional gravity-fed liquid systems can’t accommodate vertical surfaces, such as platens.
In a release, C-Sert owner Carl Strom says his company is making the installation system available at cost for around $1,000, which he says is much less than the price of a single, large magnetic drill.
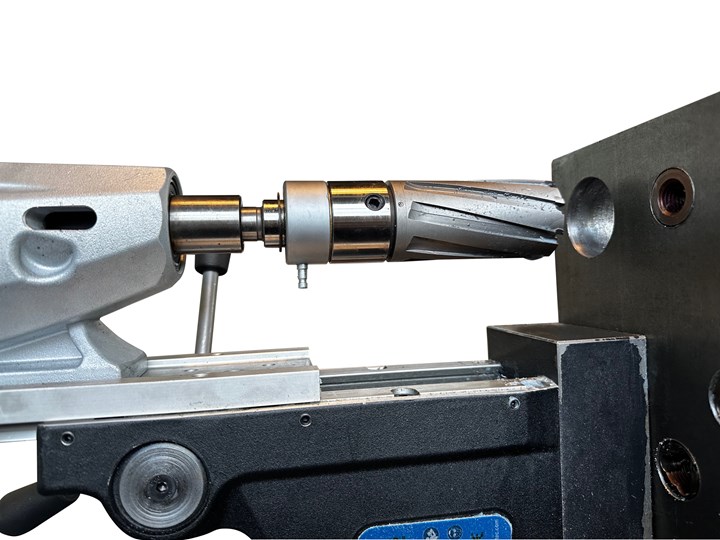
Annular cutters replace traditional drill bits for lower tool pressure. Source: C-Sert
Related Content
-
Breaking News From NPE2024
Here is a firsthand report of news in injection molding, extrusion, blow molding and recycling not previously covered.
-
Four Industry 4.0 Tech Adoption Insights from Indiana Plastics Manufacturers
As more plastics manufacturers step into the Fourth Industrial Revolution, insights have emerged about how best to approach the digital transformation journey.
-
Attending NPE2024 From the Perspective of a Molder
NPE2024 has come and gone, but before it’s completely in our collective rearview, Plastics Technology asked Rodney Davenport, vice president at injection molder CH3 Solutions, for a processor’s perspective on the big show.