Software Tracks Energy Waste in Real Time
Affordable add-on to production monitoring software alerts uses when energy is being wasted.
A new energy-waste module from Intouch Monitoring will reportedly enable manufacturers to achieve what the company calls "world-class energy-efficient production.”
As the developer explains, energy monitoring is the process of tracking, recording and visualizing energy consumption in real time across an entire facility, and getting a comprehensive overview of each line or asset for optimized performance. Energy monitoring alone does not reduce energy consumption, Intouch Monitoring points out, but having access to critical data, manufacturers can fully optimize consumption, address problem areas, change behavior and drive down costs and emissions. Up to 97% of a machines’ energy usage can be wasted while it's idle, which is a significant loss of money and resources, the company maintains.
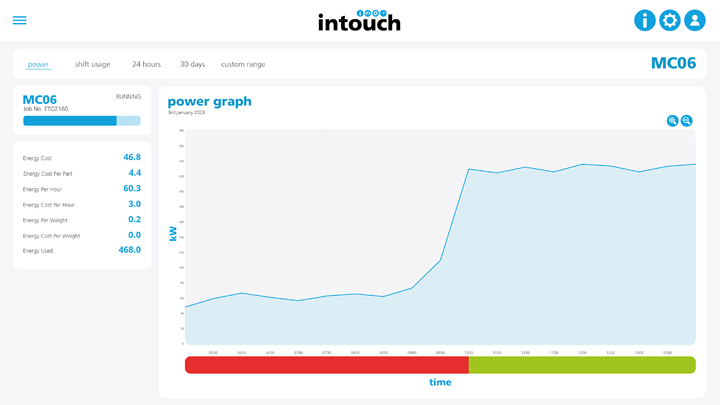
Photo: Intouch Monitoring
Notes John Hardwick, managing director at Intouch Monitoring says “Our new module gives much needed immediate notification of energy waste situations, which will deliver instant savings. If a hydraulic injection molding machine stops but the motor is left on, it could still use over 50% of what it uses when running.
The new energy monitoring module is an affordable addition to Intouch's production monitoring system, at just £5 (roughly $6) per machine per month, the developer notes.
Related Content
-
Using Data to Pinpoint Cosmetic Defect Causes in Injection Molded Parts
Taking a step back and identifying the root cause of a cosmetic flaw can help molders focus on what corrective actions need to be taken.
-
Three Key Decisions for an Optimal Ejection System
When determining the best ejection option for a tool, molders must consider the ejector’s surface area, location and style.
-
A Systematic Approach to Process Development
The path to a no-baby-sitting injection molding process is paved with data and can be found by following certain steps.