PP Impact Copolymer for TWIM Packaging
INVISTA’s new AP5197-LV PP is ‘fortified’ with Milliken’s DeltaMax performance modifier.
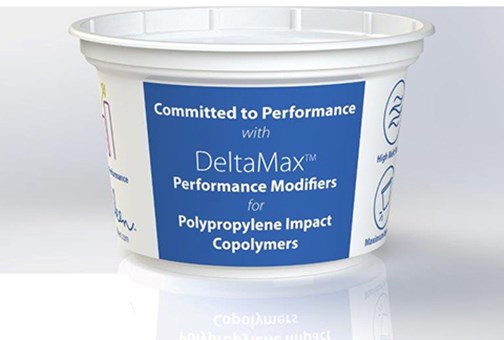
A PP impact copolymer specially developed for thin-wall injection molded (TWIM) packaging is newly available from INVISTA Polypropylene. AP5197-LV PP was joint developed with Milliken & Company using Milliken’s DeltaMax performance modifier. The new grade is FDA compliant for food-contact applications, and is well suited for refrigerated packaging such as large yogurt cups, and dip and deli salad containers.
This impact copolymer is said to surpass incumbent PP materials in TWIM packaging applications by reportedly delivering superior impact strength, high melt flow and good stiffness simultaneously, without any trade-offs typically seen among these properties. Its high melt flow rate supports thin-wall designs and increases throughput while reducing energy use while its high impact strength at low temperatures protects against breakage of refrigerated packaging when dropped by consumers or workers. Additionally, its high stiffness allows packages to be stored, transported, and shelved in taller stacks to conserve space.
Calling it another milestone in the company’s successful collaboration with Milliken, INVISTA’s director of PP R&D Pierre Donaldson said, “The balanced performance of Milliken’s additive technology enhances the resin architecture of our new AP5195-LV PP impact copolymer. By excelling in impact, melt flow and stiffness, our novel PP material can make it easier for converters to produce strong yet lightweight packaging, boost productivity, and reduce energy and plastic use to support environmental efforts.”
Related Content
-
Medical Tubing: Use Simulation to Troubleshoot, Optimize Processing & Dies
Extrusion simulations can be useful in anticipating issues and running “what-if” scenarios to size extruders and design dies for extrusion projects. It should be used at early stages of any project to avoid trial and error and remaking tooling.
-
What to Look for in High-Speed Automation for Pipette Production
Automation is a must-have for molders of pipettes. Make sure your supplier provides assurances of throughput and output, manpower utilization, floor space consumption and payback period.
-
Paperless ‘Smart Factory’ Based on Automated Production Monitoring
Tier 1 automotive molder’s home-built production-monitoring and ERP systems, designed for “the little guy,” boost its efficiency rating and profits.