Next-Generation Gear Reducer is Sleek, Robust
Can accommodate a variety of extrusion requirements, including those with high and low torque, speeds and extrusion pressures.
Davis-Standard’s next-generation gear reducer features a sleek new design and represents a commitment to customer feedback, field experience, and technical engineering while building upon the robust performance synonymous with Davis-Standard gear reducers. The new reducer fulfills a variety of extrusion requirements, including those with high and low torque, speeds and extrusion pressures. It can also accommodate the DS Activ-Check system, Davis-Standard’s Industry 4.0 platform for continuous monitoring, preventative maintenance and mobile alerts.
The new gear reducer is available in five different dimensions and capacities for extruders ranging from 2 in. (50 mm) to 6.5 in. (165mm). Reported advantages include:
Horizontal and vertical orientations : The horizontal orientation is said to be a good fit for belt-driven machines and/or low centerlines. This allows for a range of belt drives, versatile feedscrew timing, and adaptability to direct-coupled drives. The vertical housing arrangement is designed for direct-coupled and narrow footprint machines. It allows for tight positioning of extruders used in multilayer processes.
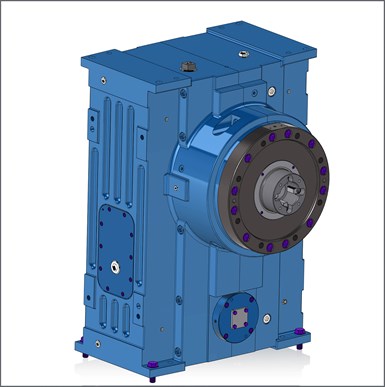
Image: Davis-Standard
Cooling and lubrication: There are two cooling and lubrication options based on housing style and customer requirements. These include oil bath lubrication and partial immersion/forced lubrication.
Gears and roller bearings: Case-hardened precision ground helical gearing is available in a wide range of gear reduction ratios to suit process requirements. New to this reducer series are spherical roller thrust bearings which absorb the axial process load and provide a self-centering, compact design with superior low-friction characteristics.
Radial shaft seals : All reducers are fitted with high-quality, spring-loaded radial shaft seals to contain lubrication oil and exclude contaminants.
Felt excluder: A felt ring excluder has been added to the front output shaft to protect the shaft and seal from abrasion and extend seal life.
Housing design: Durable cast iron construction provides quiet operation and minimal vibration. Large inspection ports simplify viewing of gear tooth condition, and a non-vented, bullet-type oil sight check eliminates the potential for leakage. Large oil fill ports allow for easier filling, while a low point drain port enables complete draining. A front thrust shaft cover completely encloses the reducer housing, allowing for more precision seal-to-shaft alignment.
Davis-Standard says the new gear case can be retrofit to older extruders in some cases.
Related Content
-
Understanding Melting in Single-Screw Extruders
You can better visualize the melting process by “flipping” the observation point so the barrel appears to be turning clockwise around a stationary screw.
-
The Importance of Barrel Heat and Melt Temperature
Barrel temperature may impact melting in the case of very small extruders running very slowly. Otherwise, melting is mainly the result of shear heating of the polymer.
-
Roll Cooling: Understand the Three Heat-Transfer Processes
Designing cooling rolls is complex, tedious and requires a lot of inputs. Getting it wrong may have a dramatic impact on productivity.