New Tool Steel Qualified for Additive Manufactured Molds and Dies
Next Chapter Manufacturing says HTC-45 — an optimized H-13 — will offer superior thermal transfer and longer tool life.
Next Chapter Manufacturing has successfully qualified HTC-45 as a new tool steel available for additively manufactured molds and dies, offering a material that it says eliminates the cracking that can be common with H-13 while also increasing thermal conductivity to twice that of maraging steel. The company announced the new offering and brought a sample printed component to the recent PTXPO (March 28-30; Donald E. Stephens Convention Center; Rosemont, Ill.).
Jason Murphy, owner and CEO Next Chapter Manufacturing, said in a release that the new HTC-45 will enable his company to push the limits of additive manufactured molds and dies by providing longer wear and tool life through better thermal transfer, which also leads to faster cycle times. Murphy told Plastics Technology that the newly qualified material behaves like copper beryllium in terms of thermal transfer but is still a steel.
Daido Steel developed DAP-AM HTC 40 and DAP-AM HTC 45 by optimizing the chemical composition of H13. International Mold Steel is the distributor of DAP-AM HTC powders. Next Chapter notes that H13 powder can be difficult to build without cracking, since the low thermal conductivity of maraging powder leads to higher thermal stress, cracking from water cooling channels and heat checking can occur on the design surface.
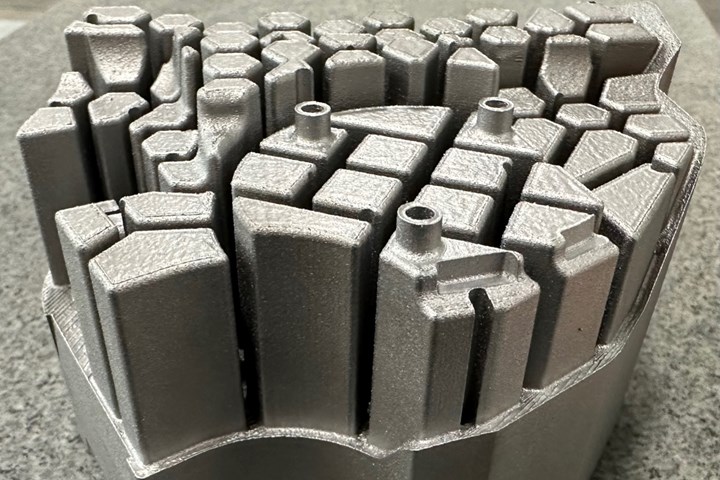
This core insert with conformal cooling channels was printed from HTC-45 powder.
Photo Credit: Next Chapter Manufacturing
Related Content
-
KraussMaffei Nears Completion of Corporate Headquarters Move
The 185-yr old German maker of plastics processing machinery is shifting to a more than 200,000-m2 greenfield site in Parsdorf.
-
Additive Technologies for Injection Mold Tooling Ride Tailwinds
NPE2024: Lowering barriers to additive manufacturing adoption in toolmaking.
-
Smooth Operators: Vibration Compensation Improves Robot Performance
Ulendo is working to apply its vibration compensation algorithm to robots. This application is more complex than its initial market of fused filament fabrication 3D printers, but could result in faster, cheaper robots.