Mixing Systems for Ultra-High Viscosity Materials
Double Planetary Mixers are well suited for mixing thick, sticky, or putty-like materials.
The ROSS line of Double Planetary Mixers, which come in a wide range of configurations and sizes ranging from ½ pint to 750 gallons, are well suited for mixing thick, sticky, or putty-like materials. The pictured Sanitary Double Planetary Mixer Model DPM-4S and Sanitary Discharge System Model DS-4S are fully customized and engineered for efficient processing of medical-grade silicone formulations in a portable workstation.
The heavy-duty, 4-gallon Double Planetary Mixer features two high viscosity “HV” stirrer blades which rotate on their own axes while orbiting the mix vessel on a common axis with a slicing motion that pushes product forward and downward and is ideal for ultra-high viscosity materials.
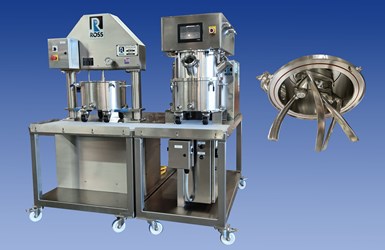
Photo: ROSS
Designed for vacuum operation, the mixer is equipped with an electromechanical lift to raise/lower the vacuum hood and a 50-psig heating/cooling jacket on the mix can. Multiple sets of vacuum hood and mix can were supplied for convenient cleaning with minimal downtime.
All product contact parts are constructed from stainless steel type 316, 150-grit finish and electropolished. Operated through a 7-inch color touch screen interface, PLC Recipe Controls deliver superior batch-to-batch consistency in the mixing of high-solids, high-viscosity applications.
The accompanying Discharge System maximizes product yield while also simplifying cleanup. It consists of a platen that is lowered hydraulically into a mix vessel. As the platen pushes down on the batch, product is forced out through a valve on the side or center bottom of the vessel with minimal product left behind. The change-can design enables semicontinuous operation, which can significantly increase production.
Related Content
-
How to Configure Your Twin-Screw Extruder: Part 3
The melting mechanism in a twin-screw extruder is quite different from that of a single screw. Design of the melting section affects how the material is melted, as well as melt temperature and quality.
-
Sirmax Adapts Integrated Recycling Approach to US Supply Conditions
Integrating compounding and recycling to leverage untapped postindustrial recycling feedstocks.
-
Configuring the Twin Screw Extruder: Part 4
For many compounding operations, material is fed to the extruder at the feed throat. This is the case when feeding a single polymer or a blend of polymers mixed with solid additives. Some ingredients, however, present a challenge in feeding. Here’s how to solve to them.