Larger Capacity Auxiliary Injection Unit Introduced
Mold-Masters has extended the capabilities of its E-Multi auxiliary injection platform, introducing the new larger capacity EM5 model.
Mold-Masters is introducing its largest capacity E-Multi auxiliary injection unit for multishot molding, the EM5. The E-Multi is an all-electric auxiliary injection unit that offers multimaterial and coinjection molding capabilities for single-shot machines. This new unit expands the shot range of the E-Multi from 550 to 1237g (18 to 42 oz).
Mold-Masters says this larger capacity system targets the production of large individual components and high-cavitation molds. Due to its size and weight, the EM5 is intended to be installed in a horizontal configuration as standard, however an optional vertical installation package is available.
The E-Multi platform converts any existing injection molding machine for multi-shot, multi-material or co-injection molding, with significantly lower capital investment requirements and faster lead times than a traditional multi-shot injection machine. E-Multi units are available from EM1 through the EM5, giving molders a broad shot range from 7.7g to 1237g (0.26 oz to 42 oz). The system is compatible with a range of plastics including post-consumer recycled resins and biobased plastics. An E-Multi for LSR is also available.
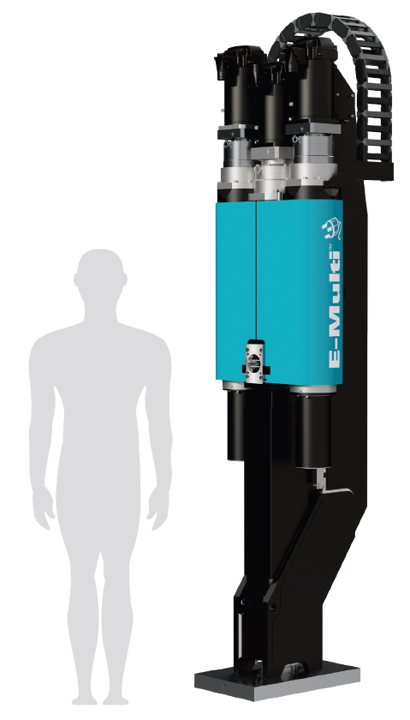
Mold-Masters newest large-capacity E-Multi auxiliary injection unit provides a shot size range from 18 to 42 oz.
Photo Credit: Mold-Masters
Related Content
-
Three Key Decisions for an Optimal Ejection System
When determining the best ejection option for a tool, molders must consider the ejector’s surface area, location and style.
-
How to Design Three-Plate Molds, Part 1
There are many things to consider, and paying attention to the details can help avoid machine downtime and higher maintenance costs, and keep the customer happy.
-
Understanding the Effect of Pressure Losses on Injection Molded Parts
The compressibility of plastics as a class of materials means the pressure punched into the machine control and the pressure the melt experiences at the end of fill within the mold will be very different. What does this difference mean for process consistency and part quality?