Large Capacity Recycling Pipe Shredder
ZRS series pipe shredder processes plastic pipes with a diameter of up to seven feet and a length of up to 23 feet.
Zerma’s most recent model of ZRS series pipe shredder can process plastic pipes with a diameter of up to 2.2 meters (7 ft.) and a length of up to 7.0 meters (23 ft.).
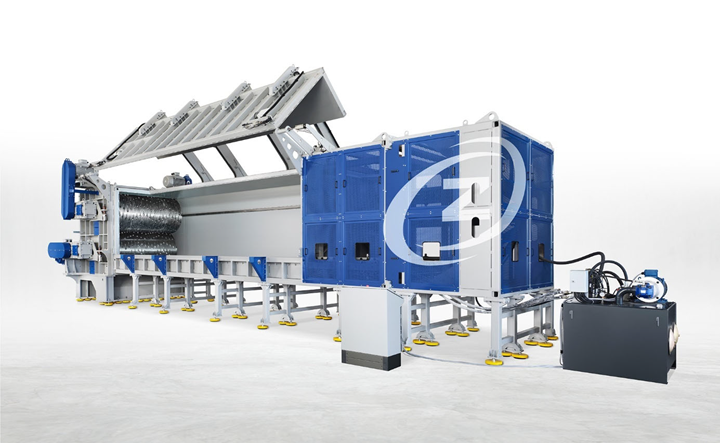
Zerma Pipe Shredder ZRS 2600
Photo Credit: Zerma
Pipes are fed in horizontally via an enclosed feeding trough. To ensure safety, the machine is switched off during loading and the area is secured by a light-grid ensuring the machine cannot be started while people or loading equipment are in the area. As soon as the heavy-duty hydraulically operated cover is closed and locked, the shredding process starts automatically. The pipes are pressed by a strong hydraulic pusher against the two rotors which are arranged vertically and rotate in the same direction. Once the pusher completes the forward stroke, it will retract, the shredder switches off and a new loading cycle can start. The feeding hopper can accept various sizes of pipes, even cascading multiple pipe diameters, optimizing the production process and increasing the overall performance of the pipe shredder.
The rotors have a diameter of 1.3 meters (4.3 ft.) and a width of 2.6 meters (8.5 ft.) and are driven by a powerful gear combination consisting of two gearboxes with 55 kW (73.8 hp) motors each.
The ZRS series pipe shredder can shred pipes with different diameters and wall thicknesses as well as pipes that are nested in one another. The machine has a control panel with separate operator panel that enables the user to monitor and control the operation. This operator panel offers a touchscreen user interface, enabling complete control and monitoring of the process.
Related Content
-
Breaking News From NPE2024
Here is a firsthand report of news in injection molding, extrusion, blow molding and recycling not previously covered.
-
Multilayer Solutions to Challenges in Blow Molding with PCR
For extrusion blow molders, challenges of price and availability of postconsumer recycled resins can be addressed with a variety of multilayer technologies, which also offer solutions to issues with color, processability, mechanical properties and chemical migration in PCR materials.
-
Foam-Core Multilayer Blow Molding: How It’s Done
Learn here how to take advantage of new lightweighting and recycle utilization opportunities in consumer packaging, thanks to a collaboration of leaders in microcellular foaming and multilayer head design.