Injection Machine Line Comes Equipped With Microcellular Foam Technology
LS Mtron’s ONE* MuCell machine line features 10 models ranging from 550 to 3600 tons and is outfitted with Trexel’s MuCell technology.
LS Mtron (U.S. headquarters Peachtree Corners, Ga.) has launched the ONE* MuCell line of injection molding machines, which come equipped with Trexel’s MuCell microcellular foam technology. LS Mtron’s South Korean parent company signed an agreement with Trexel to license its MuCell technology in 2019.
The ONE* MuCell line consists of 10 models of injection molding machines ranging in clamp force from 550 to 3600 tons. Key features include the core back function, where the volume of the mold is increased once the foamed resin has filled the cavity, causing the foam to expand, and servo valves for precision position control. Specifically, a company spokesperson told Plastics Technology that each hydraulic block has a mounted servo valve.
Addition features include KEBA controller, digital position sensors, and a specially designed screw for MuCell foaming with a 23:1 L/D ratio. LS Mtron told Plastics Technology that there are position sensors on the clamping unit, tie bars and injection unit. The digital position sensor mounted on the injection unit controls the servo valve for the most accurate back pressure. The tie bars’ digital position sensors are used control the core back function.
The company says these machines are capable of standard non-foam molding without modification, with the MuCell technology managed by a separate controller.
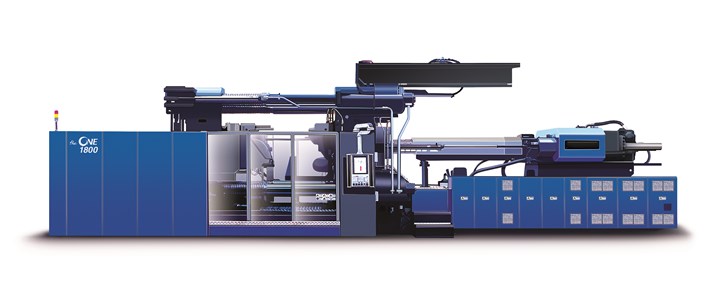
LS Mtron has introduced the ONE* MuCell line of injection molding machines, featuring 10 models ranging in clamp force from 550 to 3600 tons that come installed with microcellular foam molding capabilities.
Photo Credit: LS Mtron
Related Content
-
Understanding the Effect of Pressure Losses on Injection Molded Parts
The compressibility of plastics as a class of materials means the pressure punched into the machine control and the pressure the melt experiences at the end of fill within the mold will be very different. What does this difference mean for process consistency and part quality?
-
Three Key Decisions for an Optimal Ejection System
When determining the best ejection option for a tool, molders must consider the ejector’s surface area, location and style.
-
How to Design Three-Plate Molds, Part 1
There are many things to consider, and paying attention to the details can help avoid machine downtime and higher maintenance costs, and keep the customer happy.