High-Temperature-Resistant Plastic Targets Electric Vehicle Applications
Freudenberg Sealing Technologies says its injection-moldable thermoplastic withstood an applied flame with a temperature of 1,200°C for more than 25 minutes.
Share
Read Next
As it seeks to improve fire protection in electric vehicle drives, has developed a material called Quantix Ultra, which can resist melting even at temperatures of up to 1,200°C. The company says the thermoplastic based on grades of polyketone (PK) and polyetheretherketone (PEEK) can be processed via injection molding, and it has a lower density compared to metallic materials. Freudenberg further notes that the first series application — a flame protection barrier for cooling system parts in an electric car’s lithium-ion battery — will be used for the first time by a car manufacturer in series production vehicles in February 2024.
Freudenberg says Quantix Ultra represents a new material class that can withstand very high temperatures without melting or igniting. In laboratory tests, a 2-mm-thick material sample resisted an applied flame with a temperature of 1,200°C for more than 25 minutes.
Additional tests simulating the emission of hot particles under high pressure were also conducted, with Quantix Ultra withstanding the stress test for 20 seconds. Comparatively, a 2-mm-thick aluminum sample only took two or three seconds to be destroyed.
Freudenberg notes that once the glass transition temperature is reached for a thermoplastic, its rigidity decreases and then collapses when the melting point is exceeded. Quantix Ultra, however, doesn’t melt at high temperatures; instead, it exhibits elastic behavior comparable to elastomers, with a glass transition temperature that is 53 Kelvin higher than other PEEK-based grades. In terms of processing, a Freudenberg spokesperson told Plastics Technology that PK’s melting temperature is about 220°C with a barrel temperature of 230-240°C; while PEEK molds with a barrel temperature of 350-400°C.
Additional crosslinking of the plastic molecular chains — brought about by introducing a special crosslinking agent during injection molding — ensures that the component maintains its shape even under extreme conditions. Freudenberg says material properties can be adjusted with a focus on the specific application, which is part of its patented technology.
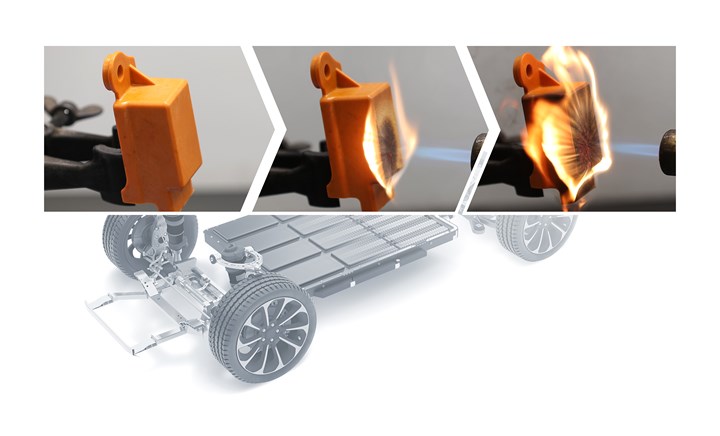
Freudenberg Sealing Technologies says its Quantix Ultra material has withstood extreme temperature testing. Photo Credit: Freudenberg
Related Content
-
How to Design Three-Plate Molds, Part 1
There are many things to consider, and paying attention to the details can help avoid machine downtime and higher maintenance costs, and keep the customer happy.
-
Back to Basics on Mold Venting (Part 1)
Here’s what you need to know to improve the quality of your parts and to protect your molds.
-
Hot Runners: How to Maintain Heaters, Thermocouples, and Controls
I conclude this three-part examination of real-world problems and solutions involving hot runners by focusing on heaters, thermocouples, and controls. Part 3 of 3.