Heated Tapered Nozzle Launches
Introduced by Zeiger and Spark Industries at the PTXPO, the nozzle is designed for maximum heat transfer and uniformity with a continuous taper for self cleaning.
Zeiger and Spark Industries have collaborated on a new heated tapered nozzle that’s designed for reduced pressure drop, self-cleaning operation and the ability to work with aggressive materials, including polysulfones and halogen-free flame retardants (HFFR). Zeiger’s Stan Glover told Plastics Technology that the nozzles, which launched at the PTXPO (March 28-30; Donald E. Stephens Convention Center; Rosemont, Ill.), are available for any and all injection molding machine brands and sizes, with a sweet spot within small- to mid-tonnage machines up to about 300 tons. The general screw diameter range the heated tapered nozzles can work with is 16 to 70 mm.
Promising maximum heat transfer and uniformity, the nozzle’s heating component, which slides over the body, is constructed from swaged stainless steel, with heating from a precision-wound, high-surface-area heating element wire featuring a replaceable thermocouple. The nozzle body is constructed from hardened PM stainless tool steel and its melt channel features a continuous taper. This design allows for self cleaning and more rapid color changes.
The design and construction materials lend the nozzle to use with polycarbonates, where it can help minimize specks and streaking, as well as sulfone resins, where its 20% chromium content alleviates sulphidation. It’s also suited for use with resins that feature HFFR additives.
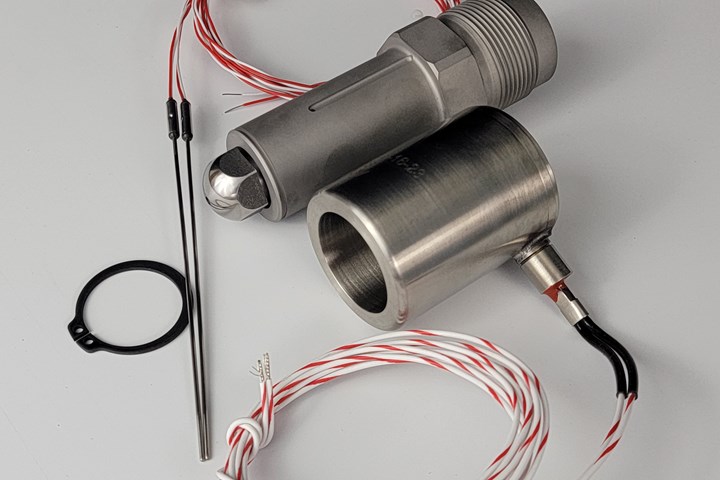
The new heated tapered nozzle features a design that allows for self cleaning of troublesome resins.
Photo Credit: Spark Industries
Related Content
-
Optimizing Pack & Hold Times for Hot-Runner & Valve-Gated Molds
Using scientific procedures will help you put an end to all that time-consuming trial and error. Part 1 of 2.
-
Back to Basics on Mold Venting (Part 2: Shape, Dimensions, Details)
Here’s how to get the most out of your stationary mold vents.
-
Is There a More Accurate Means to Calculate Tonnage?
Molders have long used the projected area of the parts and runner to guesstimate how much tonnage is required to mold a part without flash, but there’s a more precise methodology.