Fakuma: Track the Health, Performance of Hydraulic Units and Pumps
Wittmann Battenfeld says Health Factor helps molders more effectively schedule maintenance on a machine’s main hydraulic units.
Building off its condition monitoring system (CMS) introduced at K 2016, Wittmann Battenfeld introduced the Health Factor capability, which indicates the health status of the main hydraulic units, from which the condition of the pumps can be deduced.
In an injection molding machine, the clamping unit, ejector, injection unit, and the injection and metering systems are driven by the main hydraulic units, which are in turn powered by the servo-pumps, making them key to consistent, quality production.
Health Factor uses internal real-time process parameters of the drivetrain, as well as historical trend values, to determine status and performance. Wittmann notes that if the performance indicator falls for a single unit, that means that only that unit is showing wear. If, however, the performance indicators decrease for all units, that indicates a general pump or wear issue.
In addition to allowing repair and maintenance work to be planned more effectively, Health Factor lets molders sharpen their focus to a specific unit or pump. The operator can also order any required parts and schedule downtime in a way that minimizes production disruption.
When announced at K 2016, the full CMS suite monitored the drive function of the hydraulic system, including vibrations in the pump drive, power usage and system pressure. In servo-hydraulic machines, CMS diagnoses oil quality on the basis of temperature, particulate presence and water content. In all-electric machines, it assesses the quality of the gear oil.
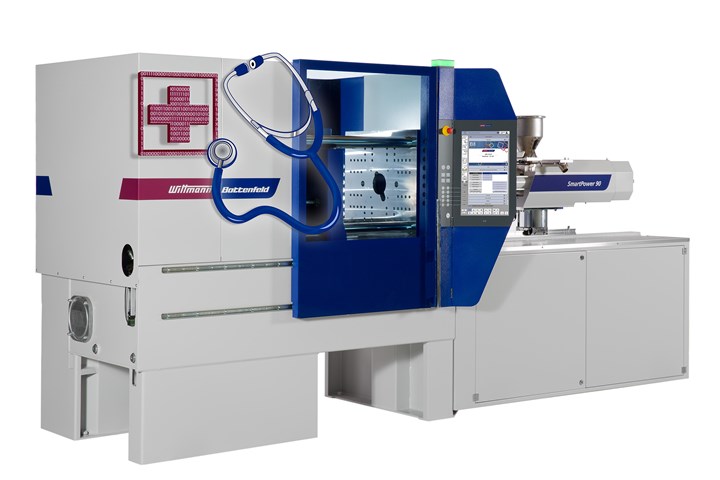
Wittmann’s CMS light Heath Factor is described as a performance indicator for the health status of hydraulically driven units and pumps.
Photo Credit: Wittmann Battenfeld
Related Content
-
PTXPO Recap: Smarter Resin Drying & Conveying Automation
Check out what you missed on the PTXPO show floor. In this video, Editorial Director Jim Callari breaks down how AI is changing the game in plastics manufacturing.
-
Digital Manufacturing: Two Medical Molders Embrace Industry 4.0
‘Digitalization’ and ‘connectivity’ are loaded terms—shorthand for a whole new way of doing 大象传媒. It can’t be accomplished in one go. But two Midwest molders in the sensitive medical field are already feeling the benefits of their initial steps in that direction.
-
Pursuing Paperless: Injection Molders Who Have Embraced Digitization
Read about injection molders who have shifted everything from quality control and scheduling to production and process monitoring to the digital realm.