Fakuma: Robot Makes Safe, Early Starts; Optimizes Path Planning
Engel is expanding its range of smart assistance systems at Fakuma 2021 adding the new iQ motion control to its viper series linear robots.
Visitors to Engel’s booth (hall A5, stand 5204) at Fakuma (Oct. 12-16; Friedrichshafen, Germany) will see the newest addition to its range of smart assistance systems: iQ motion control. iQ motion control enables Engel’s viper series linear robots to make a safe, early start and enjoy fully automatic optimized path planning. Engel says this benefits molders two times over thanks to time savings in programming and shorter production cycles.
When robot arms are able to begin moving into the mold while the platens are still in motion, cycle time savings are created. To ensure that the robot moves parallel to the platen, individual movement points, as well as the speed and acceleration of the entry movement, need to be specified during programming. In older systems, the trajectory along those individual points would be determined manually. With the new iQ motion control, however, that teaching is reportedly reduced to a few clicks, as the software calculates the optimum motion for the respective part-removal process, further reducing the overall cycle time.
To make parallel motions possible, it’s required that the molding machine and the robot share data, which is the case with Engel’s integrated system. The early start feature now integrated in iQ motion control means the robot doesn’t need to wait for the mold to open completely. The system suggests an early start position based on the robot and press parameters displayed on the iQ motion control setting screen. Engel says this allows even less experienced machine operators to take advantage of the function. The software also relies on a two-stage safety system to eliminate any possibility of a collision between the robot and the moving platen.
Starting in October, iQ motion control can be included in all new linear robots in the viper series. Regardless of the machine type or part removal process, Engel says molders will see efficiency gains, but the biggest improvements are to be had in processes with large mold-opening strokes for applications like deep housings, boxes or containers where longer mold cores feature.
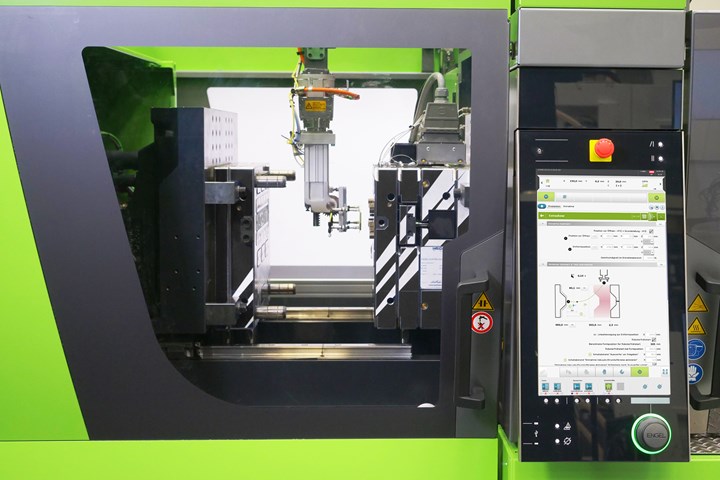
iQ motion control works with automatically optimized track planning, reducing time required for programming and machine cycle.
Related Content
-
Three Key Decisions for an Optimal Ejection System
When determining the best ejection option for a tool, molders must consider the ejector’s surface area, location and style.
-
How to Design Three-Plate Molds, Part 1
There are many things to consider, and paying attention to the details can help avoid machine downtime and higher maintenance costs, and keep the customer happy.
-
Hot Runners: How to Maintain Heaters, Thermocouples, and Controls
I conclude this three-part examination of real-world problems and solutions involving hot runners by focusing on heaters, thermocouples, and controls. Part 3 of 3.