Microcellular Foaming Paired With Specialized Screw, Process Control Program
KraussMaffei will apply its APCplus dynamic process control technology and an optimized screw with the MuCell process in Friedrichshafen.
At Fakuma KraussMaffei will demonstrate MuCell on an all-electric PX 321-1400, featuring an optimized HPS-Physical Foaming (HPS-PF) screw and the first use of its APCplus program with microcellular foaming.
The company says it created the new HPS-Physical Foaming screw with a longer three-zone area, specifically for MuCell. KraussMaffei says the screw works for all plastics — with and without fiber reinforcement — and it provides up to 30% more plasticizing capacity. This enables molders to select smaller screw diameters than before, reducing investment and operating costs for the plasticizing unit, while generating greater output.
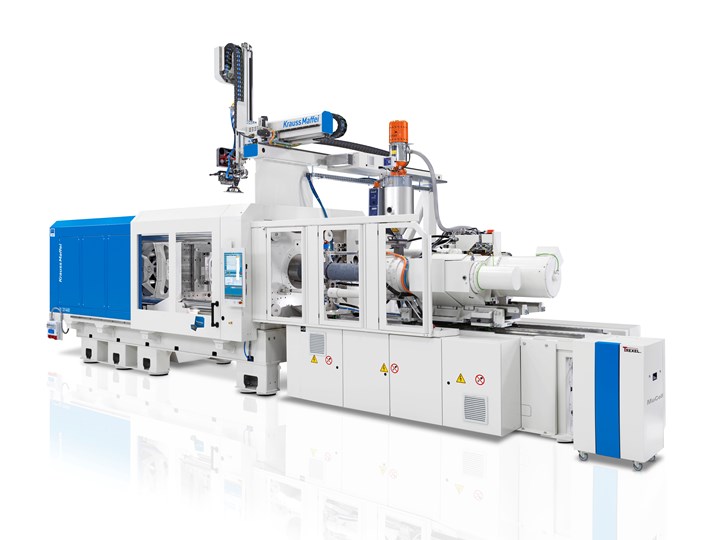
The PX 321-1400 MuCell with new universal screw with up to 30% more plasticizing capacity. Photo Credit: KraussMaffei
KraussMaffei tested variants of existing MuCell screw designs, including front and center check valves, and single-flight and double-flight three-zone areas, using a modular system. As mentioned, the APCplus machine function is being used with a gas-charged melt for the first time. APCplus shifts the changeover point and the holding pressure profile of the molding process from shot to shot based on the measured melt viscosity.
To demonstrate the technology package, KraussMaffei will create a storage table for trucks and commercial vehicles. Project partners include Isosport (Eisenstadt, Austria), which provided surface decoration via in-mold labeling. Specifically, the decorative film was required to prevent bubble formation from the outgassing nitrogen.
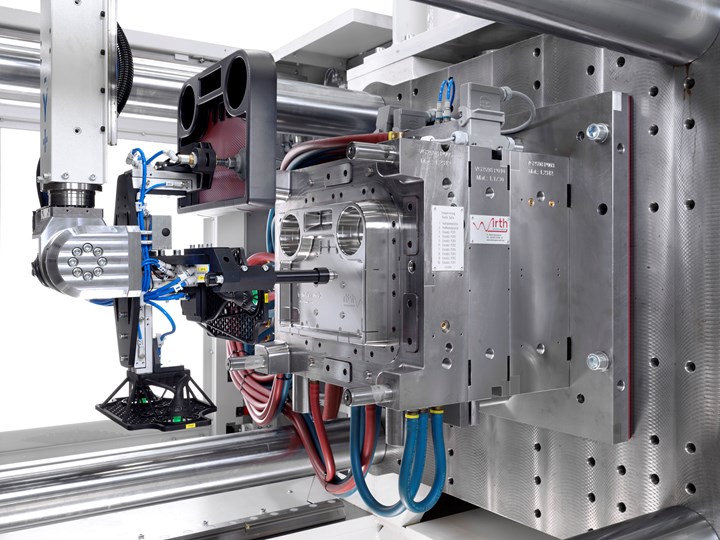
The LRX 150 linear robot removes finished parts from the mold. Photo Credit: KraussMaffei
Wirth Werkzeugbau (Helmbrechts, Germany) provided the tool, which required precise cooling to prevent what is known to the MuCell process as the post-blow effect, wherein bubbles emerge on the surfaces after molding. Specifically, special mold cooling channels were used to ensure uniform cooling at the surface, without variothermal technology, and safely prevent hot spots.
Surface effects were aided by graining technology from Reichle (Bissingen/Teck, Germany), with Lyondellbasel supplying resin. Jurke Engineering provided its Orca tempature control unit for the cell, measuring the speed and volume of coolant flow ultrasonically.
Trexel supplied the MuCell technology, continuing a collaboration with KraussMaffei that goes back to 2001. The metering system, which is fully integrated into the KM MC6 machine control, supplies the necessary gas using only one compressor.
For the process, an LRX 150 linear robot from KraussMaffei picks up the blank film from a drawer in which four different film types are stored. The robot then places the selected film on the cleaning station, where all particles and/or contaminants are removed using a cleaning brush from Wandres (Stegen, Germany) and the matching extractor system from ESTA (Senden, Germany). The robot gripper then uses clean suction cups to pick up the cleansed film.
From there, the stack gripper inserts the film into the mold and the finished part is demolded, with a “handshake” transfer to a second robot for a foam structure test using a system from Teratonics (Orsay, France). The testing system specifically enables users to visualize the compact outer layers and the spatial distribution of the MuCell foam in the interior of the component and to assess the production as free of bubbles.
All the while, the easyTrace 2.0 systems collects all process-related data, as well as the structural test for each part. A QR code that stores all process parameters for this individualized component is then created.
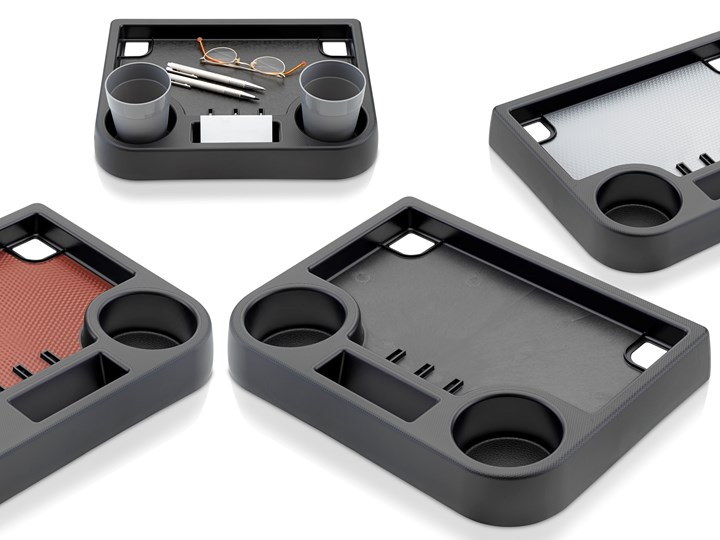
At Fakuma, the PX 321-1400 molds a storage table for trucks in four different designs utilizing MuCell. Photo Credit: KraussMaffei
Related Content
How to Design Three-Plate Molds, Part 1
There are many things to consider, and paying attention to the details can help avoid machine downtime and higher maintenance costs, and keep the customer happy.
Read MoreGot Streaks or Black Specs? Here’s How to Find and Fix Them
Determining the source of streaking or contamination in your molded parts is a critical step in perfecting your purging procedures ultimately saving you time and money.
Read MoreUse These 7 Parameters to Unravel the Melt Temperature Mystery
Despite its integral role in a stable process and consistent parts, true melt temperature in injection molding can be an enigma. Learning more about these seven parameters may help you solve the puzzle.
Read MoreProcess Monitoring or Production Monitoring — Why Not Both?
Molders looking to both monitor an injection molding process effectively and manage production can definitely do both with tools available today, but the question is how best to tackle these twin challenges.
Read MoreRead Next
Modular Screw Optimized for Microcellular Foam Molding
KraussMaffei says its HPS-Physical Foaming screw features a universal design and 30% higher plasticizing capacity for MuCell molding.
Read MoreKraussMaffei Invests in Future Plastics Professionals
KM is doing its part through machinery donations, as well as co-op and apprentice programs.
Read MoreTrexel Forming Global Network For MuCell Engineering Support
Taking a more direct role in part, tool, and process design for specific applications.
Read More