Fakuma 2023: High-Speed Pipette Tip Molding
Sumitomo (SHI) Demag, Hekuma and Schöttli partnered on production cell molding pipette tips from a 32-cavity mold in a cycle of 4.5 seconds.
At Fakuma 2023, Sumitomo (SHI) Demag presented a high-speed pipette-tip molding cell, partnering with Schöttli on tooling and Hekuma on the take-out system. Presented at Hekuma’s booth using a Sumitomo Demag IntElect S 100 molding machine, production came from a 32-cavity mold applying a proprietary 8-cavity cluster technology and 8-Star hot runner nozzles. The hot runner was designed for better melt balance, drool-free startups and fast cycles.
Schöttli noted that the process requirements dictated superior venting and cooling, in addition to the specialized hot runner. The tool also applies Schöttli’s Core Adjustment System for concentric pipettes with uniform wall thickness. The normal cycle time of 4.9 seconds was cut to 4.5 seconds because of the high-speed Hekuma take-out system, which clears the mold more quickly than if the tips just dropped from the machine. The company notes that for a 32-cavity mold, every tenth of a second in cycle reduction results in up to 4 million more parts molded annually. The cell also satisfies ISO Class 8 cleanroom standards.
Schöttli said its cluster technology is an evolution of its Side-Gate hot runner. In the new technology, each cluster has eight accessible and individually exchangeable cavities. Using the dedicated disassembly device, the cold-side cluster can be removed and handled safely while still on the press, granting access to the individually adjustable cores.
Schöttli says even that though some core displacement during injection is needed to meet the concentricity requirements of the tips, the core and bushing are fully aligned while closing the mold to avoid wear. Schöttli has long supplied open side gates that feature drool-free startup.
The 8 Star Nozzle was designed and manufactured in the Swiss Medical Center of excellence, with every mold featuring an individual design and nozzle geometry for excellent cavity balancing and optimized vestiges from the gate.
To optimize the cooling and venting concept, every core with its preassembled cooling tube is individually tested before delivery, while a maintenance-friendly venting design aims to keep uptime up and quality high.
From the machine’s perspective, Sumitomo (SHI) Demag says the 32-cavity pipette tip mold requires high injection speeds, with precise control of ramp-up and ramp-down of these speeds, which the machine maker says is made possible by its highly dynamic direct drive.
Only 0.14 second is required to reach the IntElect’s maximum injection speed of 350 mm/sec. For pipette tips (which feature long, thin core pins), filling at those high speeds can actually help prevent core shifts. With slower injection speeds, the cooling of material as it enters the cavity can be exacerbated by the narrowing of the melt channel. To overcome this, higher injection pressures are normally used, which increase overall energy usage and may force the molder to switch to a higher tonnage machine.
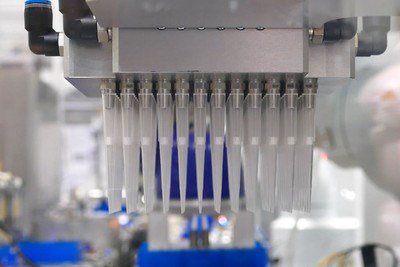
A production cell at Fakuma 2023 molded pipette tips using automation to reduce cycle times and advanced hot runners for part concentricity. Photo Credit: Sumitomo (SHI) Demag
Related Content
-
Optimizing Pack & Hold Times for Hot-Runner & Valve-Gated Molds
Using scientific procedures will help you put an end to all that time-consuming trial and error. Part 1 of 2.
-
Injection Molding: Focus on these Seven Areas to Set a Preventive Maintenance Schedule
Performing fundamental maintenance inspections frequently assures press longevity and process stability. Here’s a checklist to help you stay on top of seven key systems.
-
Back to Basics on Mold Venting (Part 1)
Here’s what you need to know to improve the quality of your parts and to protect your molds.