Extrusion: New Extruder Line Targets Medical Applications
Series comes with a range of standard features. Customization also available.
US Extruders has introduced a new series of extruders specifically for the medical market. The machine builder, based in Westerly, R.I. rolled out the Med-Ex line of medical extruders during the Plastec West trade show held Feb. 11-13 in Anaheim, Calif.
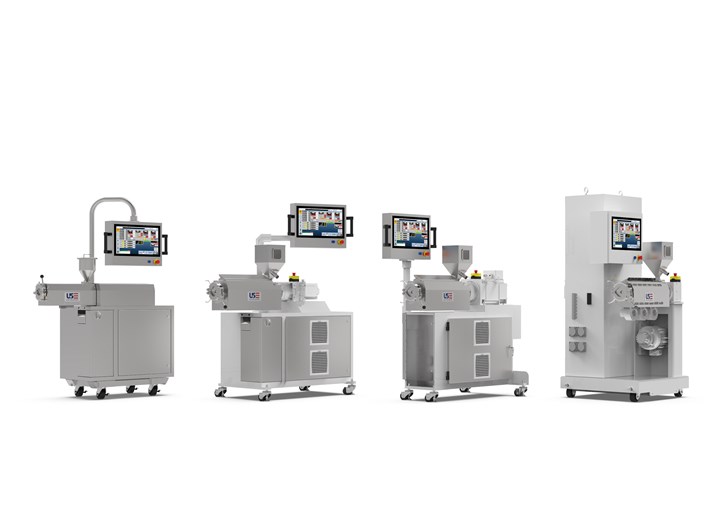
The line comes in four iterations:
Med-Ex Elite: Key features (photo left) include easy-to-swap barrels (0.5 in. to 1 in.); stainless steel surfaces that can be easily wiped down; easy open and close toggle clamps; a temperature range to 900 F; precision servo moto; corrosion-resistance design option; clean wire management; arc flash NFPA 70 E compliant; and virtual pressure measurement.
Med-Ex Elite Flex: Key features (photo second left) include swappable barrels (0.5 in. to 1 in., or 0.75 in. to 1.25 in.); easy open and close toggle clamp; precision servo motor; a temperature range to 900 F; corrosion-resistance design option; clean wire management; arc flash NFPA 70 E compliant; and low-profile casters with integral jacking pads.
Med-Ex Compact: Key features (photo second right) include a slim panel design, gearless direct drive; easy open and close toggle clamps; a temperature range to 900 F; precision servo moto; corrosion-resistance design option; clean wire management; arc flash NFPA 70 E compliant; a clear-covered plug plate; and low-profile casters with integral jacking pads.
Med-Ex Classic: Key features (photo right) include an economical design; easy open and close toggle clamp; base-mounted cabinet; and air or water cooling.
Extruders can be equipped with the firm’s ProControl Medical touch screen control system offering recipe management, data acquisition, reporting, and alarm analytics. Discrete controls tailored to specifications can also be provided.
Related Content
-
How to Select the Right Tooling for Pipe Extrusion
In pipe extrusion, selecting or building a complementary set of tooling often poses challenges due to a range of qualitative factors. Here’s some guidance to help you out.
-
Extrusion Excellence: This Year's Top Stories
Revisit the year’s most popular articles on extrusion technology and processes, showcasing innovations, best practices, and the trends that captured the plastics processing community’s attention.
-
Medical Tubing: Use Simulation to Troubleshoot, Optimize Processing & Dies
Extrusion simulations can be useful in anticipating issues and running “what-if” scenarios to size extruders and design dies for extrusion projects. It should be used at early stages of any project to avoid trial and error and remaking tooling.