Energy-Efficient Bottle Blowing with PCR
At K 2022 this month, W. Müller is presenting a system for PCR processing in a three-layer coextrusion, using an energy-saving barrel-heating system.
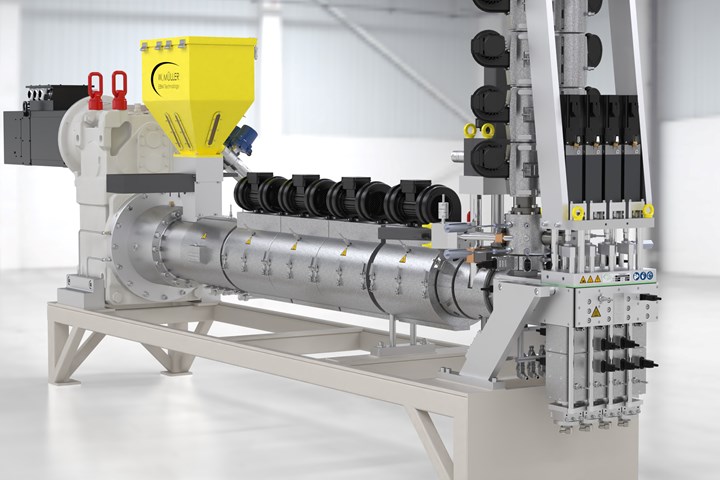
W. Müller’s ReCo3 system at K 2022 coextrudes a three-layer parison with a PCR core. Two vertical extruders for the thin virgin inner and outer layers are mounted over the head. Particularly interesting is the more compact and energy-saving barrel heating system with aluminum heating tapes instead of ceramic heaters. (Photo: W. Müller)
In line with the show’s emphasis on sustainability and the circular economy, W. Müller will be highlighting its experience with processing post-consumer recycle (PCR) at K 2022 this month in Düsseldorf. The company will present a ReCo3 system designed specifically for processing PCR in the core of a three-layer coextrusion sandwiched between thin layers of virgin resin.
An interesting feature of this system is a energy-saving barrel heating/cooling system supplied by Austrian heating specialist (also exhibiting at K). The system uses standard air-cooling fans plus special heating tapes made of aluminum instead of the usual ceramic. The metal tapes are said to be more stable, and to distribute heat energy more quickly. This modified heating/cooling combination saves around 2000 W in this application, according to W. Müller, and the energy is distributed over the entire area, but the unit does not get hot on the outside, enhancing worker safety. What’s more, it is considerably more compact than conventional heating tapes, the company states.
Related Content
-
Get Color Changes Right In Extrusion Blow Molding
Follow these best practices to minimize loss of time, material and labor during color changes in molding containers from bottles to jerrycans. The authors explore what this means for each step of the process, from raw-material infeed to handling and reprocessing tails and trim.
-
Medical Molder, Moldmaker Embraces Continuous Improvement
True to the adjective in its name, Dynamic Group has been characterized by constant change, activity and progress over its nearly five decades as a medical molder and moldmaker.
-
Foam-Core Multilayer Blow Molding: How It’s Done
Learn here how to take advantage of new lightweighting and recycle utilization opportunities in consumer packaging, thanks to a collaboration of leaders in microcellular foaming and multilayer head design.