Electric Roller Suited for High-Temp Web Applications
Billed as “game-changing” product to enhance process control and efficiency.
Webex’s Electric HTR Roller has been designed to address the unique needs of industries requiring high-temperature applications. It boasts several features that Webex, a Maxcess company, says make it a game-changer for manufacturers looking to achieve precise process control and efficiency.
Key Features of the Webex Electric HTR Roller:
Even Heat Profile: The Electric HTR Roller offers an even heat profile end-to-end, ensuring consistent temperature distribution across the entire roll face, which is essential for high-quality production.
Multiple Heating Zones: With multiple heat zones, the Electric HTR Roller accommodates various web widths, enabling manufacturers to optimize their processes.
Fast Ramp-Up Time: The Electric HTR Roller achieves process temperatures of up to 850°F in approximately 1 hour, significantly reducing downtime and improving overall productivity.
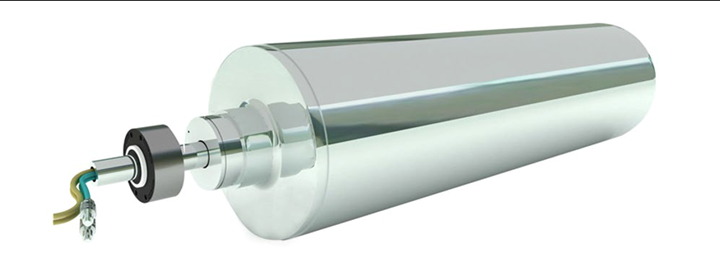
Integrated Zone Temperature Control: Featuring integrated zone temperature control with high alarm shutoff, the Electric HTR Roller offers enhanced safety and precision.
Compatibility: The Electric HTR Roller seamlessly integrates with existing controllers, providing a hassle-free upgrade option for manufacturers. Alternatively, customers can request Webex to supply compatible controllers.
Reduced Maintenance: This environmentally-friendly solution reduces maintenance costs and downtime, offering long-term benefits to users.
Energy Efficiency: The Electric HTR Roller provides up to 70% energy savings compared to traditional fluid-heated rolls, making it a cost-effective choice for 大象传媒es.
Notes Jason Annes, global product manager at Maxcess, “The Webex Electric HTR Roller represents a major advancement in the web handling industry. With its precision control, fast ramp-up time and energy efficiency, manufacturers in various industries can expect improved productivity, reduced operational costs and superior product quality.”
Related Content
-
Reduce Downtime and Scrap in the Blown Film Industry
The blown film sector now benefits from a tailored solution developed by Chem-Trend to preserve integrity of the bubble.
-
Medical Tubing: Use Simulation to Troubleshoot, Optimize Processing & Dies
Extrusion simulations can be useful in anticipating issues and running “what-if” scenarios to size extruders and design dies for extrusion projects. It should be used at early stages of any project to avoid trial and error and remaking tooling.
-
What to Know About Your Materials When Choosing a Feeder
Feeder performance is crucial to operating extrusion and compounding lines. And consistent, reliable feeding depends in large part on selecting a feeder compatible with the materials and additives you intend to process. Follow these tips to analyze your feeder requirements.