Deflection Elbow Kits for Silo-Top Fill Lines
Allows direct replacement of silo top elbows and piping/tubing, with all preparation done safely at ground level.
New Smart Elbow Deflection Elbow Kits from HammerTek Corp. allow direct replacement of silo top elbows and piping/tubing subject to abrasive wear, with all preparation done safely at ground level.
Each kit contains all components required to replace failing elbows, including two Smart Elbow deflection elbows and all necessary piping/tubing, connectors and gaskets. All can be assembled on the plant floor prior to silo top installation, reducing personnel hazards associated with maintenance at high elevations in all weather conditions.
Silo top sweep elbows are prone to failure due to large volumes of conveyed material impacting the elbow wall at high speed to change direction, causing abrasive materials to wear through the elbow wall, resulting in blow-outs and lost production due to downtime.
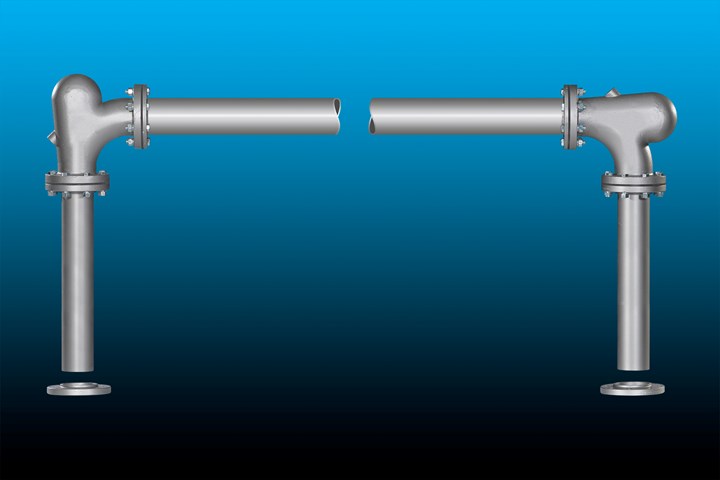
Photo: Hammertek
The Smart Elbow design features a spherical chamber that protrudes partially beyond the 90° flow path, causing a loose ball of airborne material to rotate in the same direction as the airstream that powers it, gently deflecting incoming material around the bend without impacting the elbow wall.
Socket style no-weld kits for all popular pipe and tube diameters include: two HammerTek elbows; one horizontal pipe or tube section; two vertical pipe or tube sections; and four sleeve couplings with reducer gaskets.
Flanged style kits for all popular pipe and tube diameters include: two ANSI flanged HammerTek elbows; one horizontal pipe or tube section with one welded ANSI flange; two vertical pipe or tube sections each with one welded ANSI flange; three loose ANSI flanges (for welding safely at ground level); and four gaskets.
In addition to preventing elbow wear and failure, the design reportedly precludes friable materials from degrading and dusting, plastics from melting and forming streamers, and heat-sensitive materials from building up and plugging, while reducing pressure drop and offload times by up to 50%.
Related Content
-
ACS Group Adds Regional Sales Manager
Richard Gutierrez named Southwest regional sales manager.
-
Finding Efficiencies in How Components Work Together
Auxiliary systems are vital to the proper functioning of a plastic processing line, and they can be a source of major cost and efficiency improvements.
-
Radar Level Sensor Streamlines Bulk Material Inventory Management
NPE2024: The NCR-86 is designed to ensure rapid data updates, enhancing efficiency in inventory management.