Conveyor Controller Ideal for Expanding Plants
Billed as the most flexible and reliable discrete wired conveying controller on the market.
AEC has added a distributed I/O package (DiO) to its VacTrac Plus series of conveying controllers in an effort to help processors get more from their production operation, especially when they expand their plant.
Introduced at March’s trade show, the VacTrac Plus DiO is a material- conveying control system for medium to large applications. Processors that need to control the operation of growing systems of pumps and receiver stations can harness the power of DiO by adding distributed I/O panels to the main VacTrac Plus panel via Ethernet. Also, DiO network panels can be added to ensure robust communication when Ethernet runs are longer than 300 ft.
VacTrac Plus controls vacuum receivers, vacuum pumps, remote proportioning valves, purge valves, knife gates, and pump or hopper blowback. It can be used in any type of plastic process.
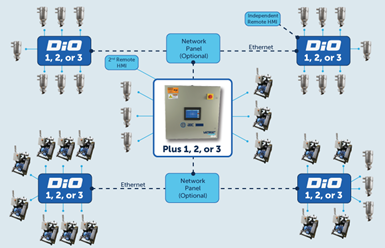
Photo: AEC
The number of pumps and receiver stations is customizable; units can be seamlessly upgraded by adding the required I/O modules and new software. DiO is said to be an ideal cost-effective solution for the largest plants thanks to users’ ability to control up to 24 pumps, 100 stations and up to 50 purge valves.
Reconfiguring factory communications is said to be easy with VacTrac Plus DiO, as it automatically detects and reconfigures I/O when new pumps or stations are installed. When expanding your network with DiO panels over Ethernet, the system automatically configures and assigns I/O.
To simplify conveying management even further, VacTrac Plus features a high-resolution, 7-in. color touch screen and Allen Bradley PLC for easy operation and monitoring. And, automatic email alerts can be set up to provide operators instant visibility into specific issues on the production floor.
What’s more, VacTrac Plus can now be remotely monitored with the ACS Group’s MiVue manufacturing insight service.
Related Content
-
How to Effectively Reduce Costs with Smart Auxiliaries Technology
As drying, blending and conveying technologies grow more sophisticated, they offer processors great opportunities to reduce cost through better energy efficiency, smaller equipment footprints, reduced scrap and quicker changeovers. Increased throughput and better utilization of primary processing equipment and manpower are the results.
-
PTXPO Recap: Smarter Resin Drying & Conveying Automation
Check out what you missed on the PTXPO show floor. In this video, Editorial Director Jim Callari breaks down how AI is changing the game in plastics manufacturing.
-
Processors: Gear Up to Handle More Regrind
Plastics auxiliary and primary processing equipment was optimized for running pellets; here’s how you can adjust to the bulk density differences of flake and regrind in drying, conveying, mixing, feeding and processing.