Continuous Machine, Process Monitoring
Provides critical and timely information for processors to improve overall line performance and plan scheduled maintenance activities.
By harnessing the value of digital transformation and smarter processing, Davis-Standard has developed technology for improving productivity gains: the DS Activ-Check system for continuous machine and process monitoring.
This cloud-based IIoT platform reportedly improves extrusion line operation and product quality for meaningful bottom-line impact. DS Activ-Check employs analytical tools and process technology algorithms to support real-time process monitoring and preventative maintenance. Operators, process engineers and production management are alerted to issues before they happen, preventing unnecessary downtime and supporting end-product consistency. Customers receive notifications via e-mail or text, and continuous monitoring of machine status is available on smart devices and remote PCs.
Examples of key machine components monitored include the extruder gearbox, lubrication system, motor, drive power unit, barrel heating and cooling functions. Monitoring of other process line parameters can be customized based on customer requirements.
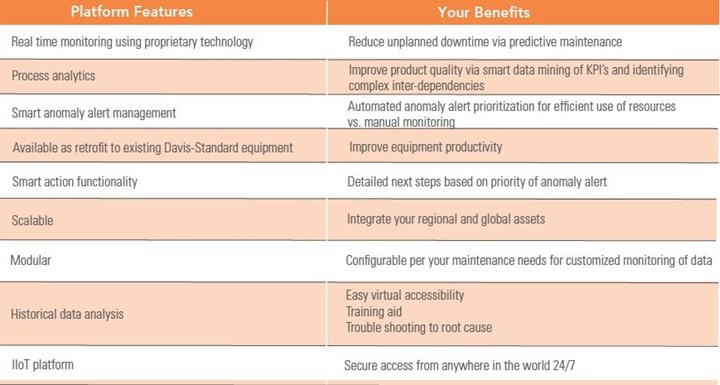
Davis-Standard says it has taken special care to ensure DS Activ-Check is easy to use. The system’s operator-friendly overview screens provide a quick reference of monitor points and data windows with a graphic indication of measurements. Operators can touch a location to view details or take advantage of on-screen formatting for e-mail or text notifications. High-level digital security and customizable application configurations provide protected accessibility.
The greatest benefit of DS Activ-Check is that it provides critical and timely information for processors to improve overall line performance and plan scheduled maintenance activities. This is essential to improve efficiencies during all phases of production. Having the capability to monitor extrusion line variables such as mechanical and electrical system conditions brings products to market faster and minimizes process interruptions.
Davis-Standard will be participating at the , September 21-23, Rosemont, Ill.
Related Content
-
The Importance of Barrel Heat and Melt Temperature
Barrel temperature may impact melting in the case of very small extruders running very slowly. Otherwise, melting is mainly the result of shear heating of the polymer.
-
Roll Cooling: Understand the Three Heat-Transfer Processes
Designing cooling rolls is complex, tedious and requires a lot of inputs. Getting it wrong may have a dramatic impact on productivity.
-
Why Are There No 'Universal' Screws for All Polymers?
There’s a simple answer: Because all plastics are not the same.