Bulk-Bag Filler Can Accommodate Wide Materials Range
Suited for powders, granules, pellets, and other bulk materials, even materials with high bulk densities.
has introduced a bulk bag filling station (BBF) designed to fill flexible intermediate bulk containers (FIBC) and other big bags safely and easily. The new AFC BBF features a rugged, steel support structure that handles fill weights up to two tons to accommodate a wide range of powders, granules, pellets, and other bulk materials, even materials with high bulk densities. The versatile bag filling machine fits bag sizes ranging from 36-in.3 cubes to 48-in.3 cubes and quickly adjusts to fit changing bag heights, widths and capacities.
Semi-automated for high efficiency, the bag filling machine includes a built-in bag inflation system as standard that establishes a secure seal between the fillspout and bulk bag to mitigate dust exposure. Prior to loading the bulk material, the prefill system fills the bag with air to prevent any potential bag creasing and ensure plastic liners fully conform to the shape of the bulk bag. The capacity of the sack is fully maximized as a stable, safe load while the workplace remains protected from dust and spillage.
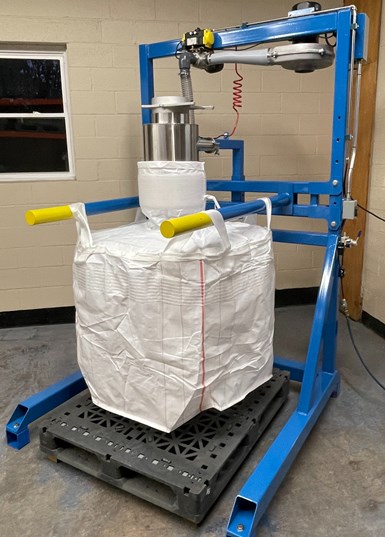
Photo: Automated Flexible Conveyor
Available with the company's Spiralfeeder flexible screw conveyor as a companion for metering material into the bulk bag filler, the new bag filling machine is offered with a wide selection of optional accessories to suit virtually any installation including integrated weighing systems and densifiers.
Related Content
-
Deflection Elbows Eliminate Streamers for Large Film Processor
New elbows eliminate troublesome streamers to increase productivity at leading blown film processor.
-
Industry Vet Duff Joins ACS Group
With 37 years of experience on both machinery and processor side, Michael Duff to handle aftermarket 大象传媒 for auxiliary equipment manufacturer.
-
PTXPO Recap: Smarter Resin Drying & Conveying Automation
Check out what you missed on the PTXPO show floor. In this video, Editorial Director Jim Callari breaks down how AI is changing the game in plastics manufacturing.