Auxiliaries: Sensor Kits Enable Non-Computer-Controlled Auxiliaries to Connect to Cloud Platform
User-installed sensor kits are now available for use not only with Conair auxiliaries on the SmartServices platform, but with a range of competitive auxiliary equipment.
New SmartServices sensor kits from Conair now make it possible to connect operating, performance, and alarm data from non-computer controlled auxiliary equipment to the SmartServices platform, Conair’s cloud-based Industry 4.0 solution for auxiliary equipment monitoring, management, and analysis.
The user-installed sensor kits are now available for use not only with Conair auxiliaries, but with a range of competitive auxiliary equipment including:
- Temperature control units (TCU);
- Positive-displacement vacuum-conveying pumps;
- Single- and dual-stage regenerative vacuum pumps;
- Portable loading/conveying systems and
- Desiccant dryers
These kits were created by Conair so auxiliary equipment that does not utilize computerized controls could be equipped with digital sensors and communications capabilities and linked to the cloud-based SmartServices platform with the same ease as newer equipment. Each user-installed kit contains common digital hardware, plus fluid-system fittings, sensors, and wiring specific to the equipment type. Digital hardware includes a SmartServices expansion box that receives sensor inputs via wiring and a SmartServices hub that securely exchanges data, via the facility’s local network, with the cloud-based analytics platform.
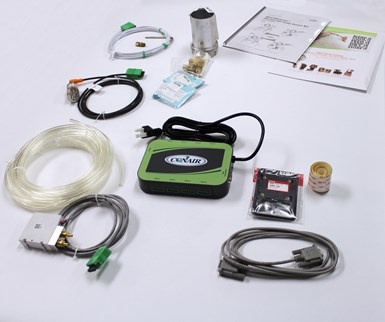
After installation, the new sensors monitor the performance and operating/maintenance status of each auxiliary, collecting data and operating information specific to the auxiliary type. For example, sensors on the TCU can monitor coolant pressure, temperature, and flow rates, while those on vacuum pumps and conveying systems will monitor air flows and speeds, vacuum levels, and the like. At the same time, sensors will also monitor for operating alarms, track maintenance alerts, and observe the vibration and temperature status of motors for anomalies that could signal possible problems.
Related Content
-
Four Industry 4.0 Tech Adoption Insights from Indiana Plastics Manufacturers
As more plastics manufacturers step into the Fourth Industrial Revolution, insights have emerged about how best to approach the digital transformation journey.
-
Better Manufacturing Data Empowers Plastics Processors to Make Better Decisions
What’s needed to take all the data pulled from production planning, production monitoring and quality control systems and put it in the hands of the right people at the right time?
-
PTXPO Recap: Smarter Resin Drying & Conveying Automation
Check out what you missed on the PTXPO show floor. In this video, Editorial Director Jim Callari breaks down how AI is changing the game in plastics manufacturing.